Case studies
1. demonstration cleaning
Six circuits were selected for presentation. Before cleaning, an inspection of the condition of the ducts was performed using an endoscopic camera.
The circuits were then tested for leaks and patency using compressed air. The mold showed no leaks.
The condition of the canals before and after
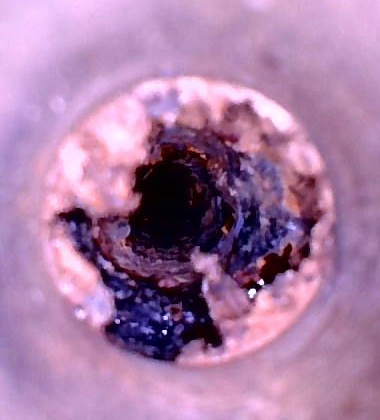
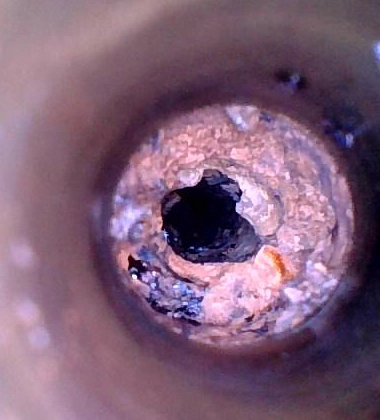
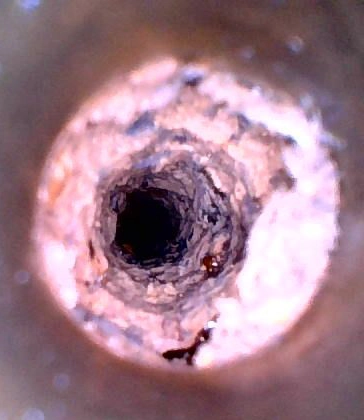
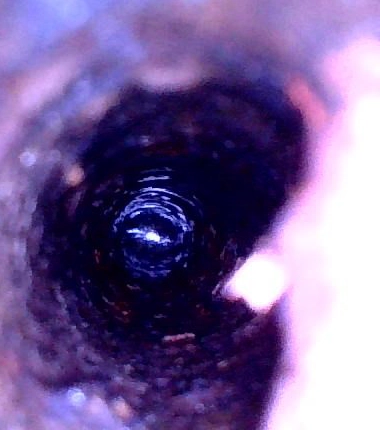
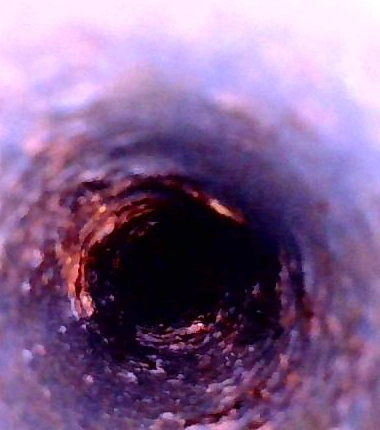
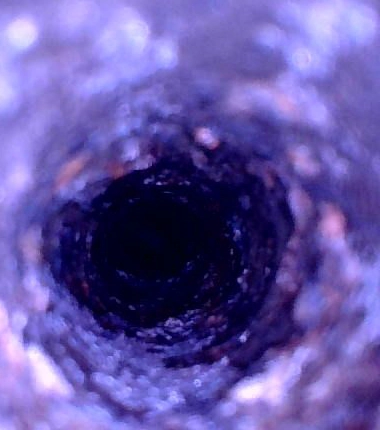
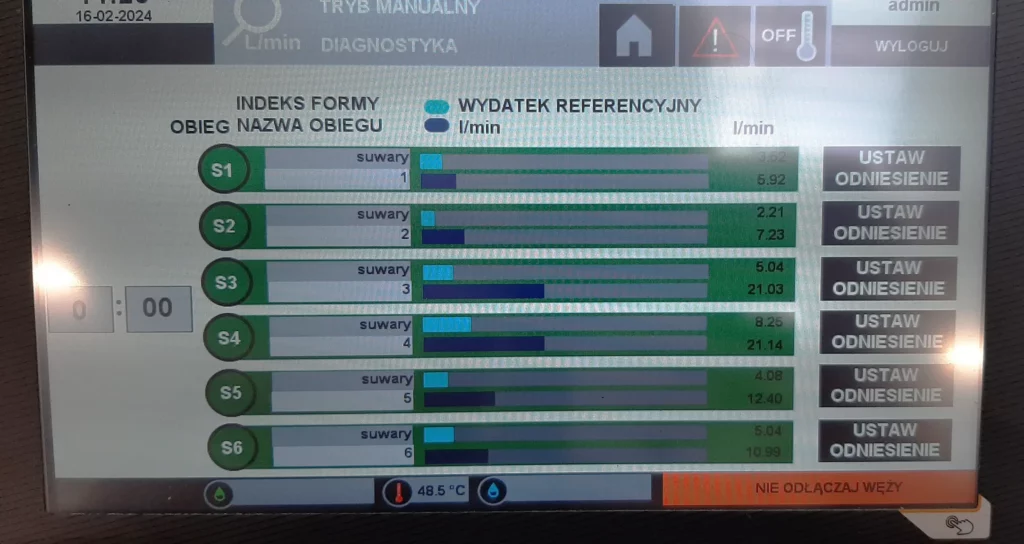
Cleaning results
The cleaning took two hours and fifteen minutes. DS2 cleaner was used for cleaning.
After the cleaning was completed, the system was purged with compressed air and flow rate diagnostics were performed for each of the individual circuits.
A comparison of flow expenses before and after cleaning is shown in the table opposite.
Channel name | Output before cleaning [L/min]. | Output after cleaning [L/min]. | Flow increase [L/min]. | Growth [%]. |
---|---|---|---|---|
1 | 3,52 | 5,92 | 2,4 | 68,18 ↑ |
2 | 2,21 | 7,23 | 5,02 | 227,15 ↑ |
3 | 5,04 | 21,03 | 15,99 | 317,26 ↑ |
4 | 8,25 | 21,14 | 12,89 | 156,24 ↑ |
5 | 4,08 | 12,40 | 8,32 | 203,92 ↑ |
6 | 5,04 | 10,99 | 5,95 | 118,06 ↑ |
2. tobacco filler component
Two-cavity mold
Forming inserts - steel 1.2709
Injection-molded material - POM
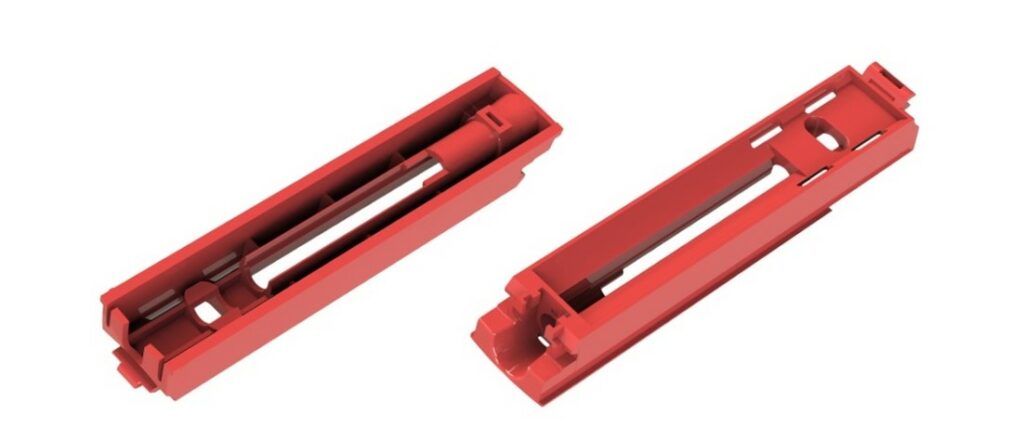
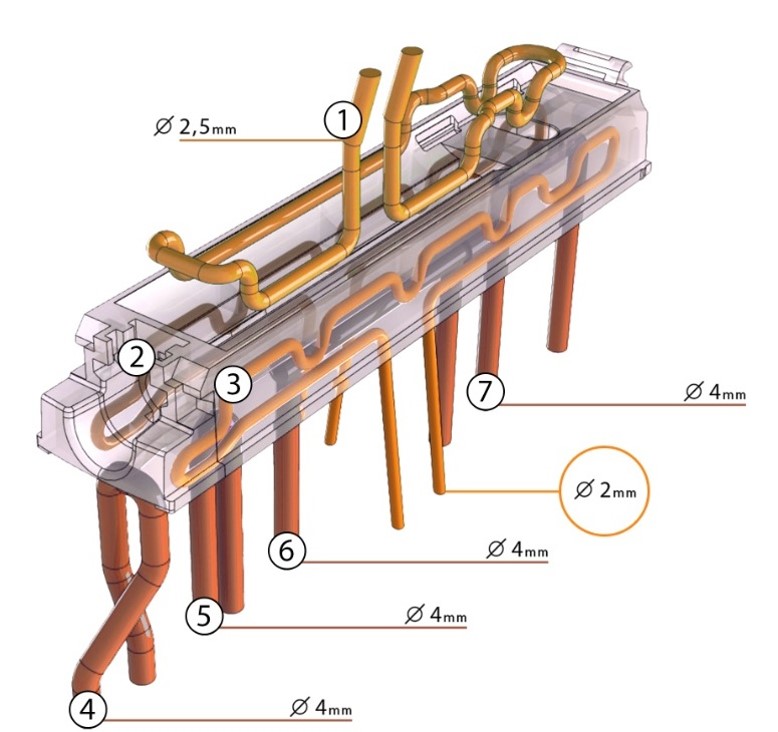
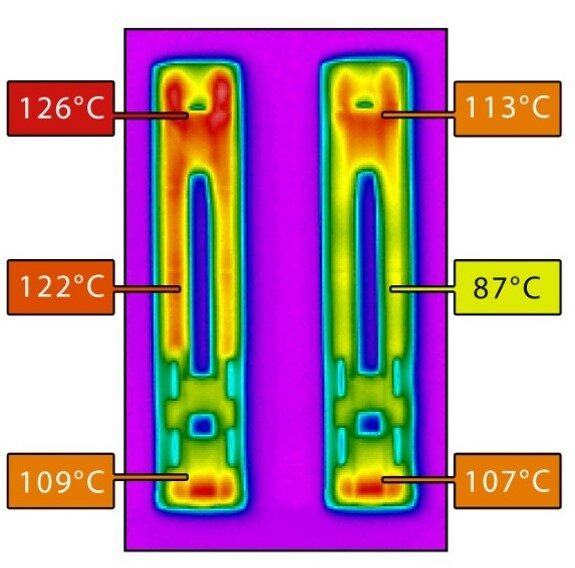
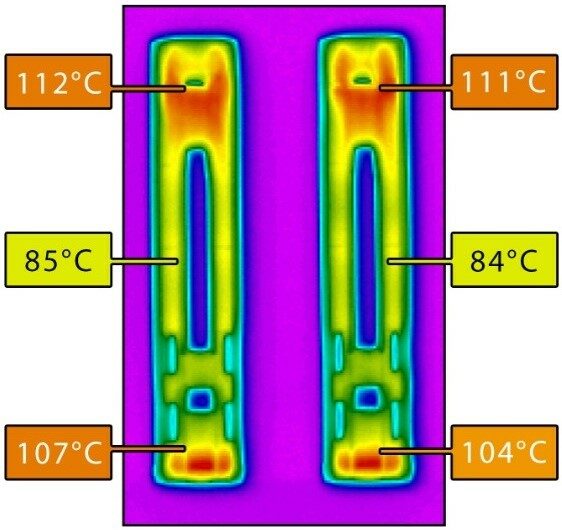
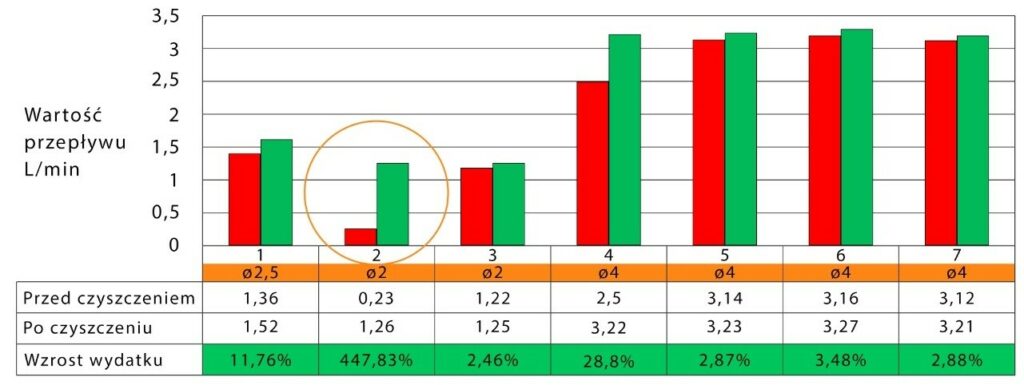
3. shutter drive system housing
Two-cavity mold
Forming inserts - steel 1.2343
Injected material - PS HIPS
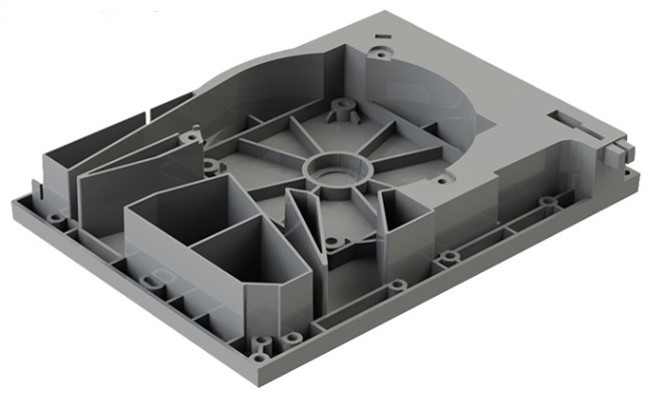
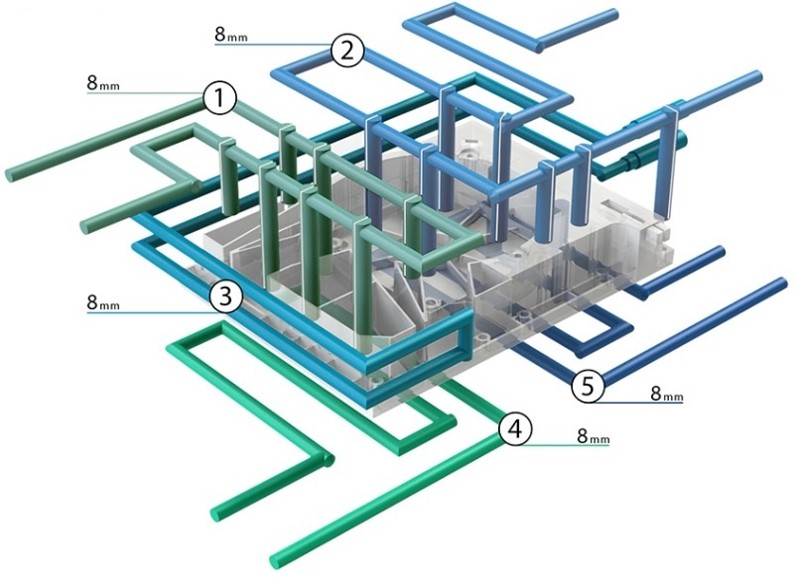
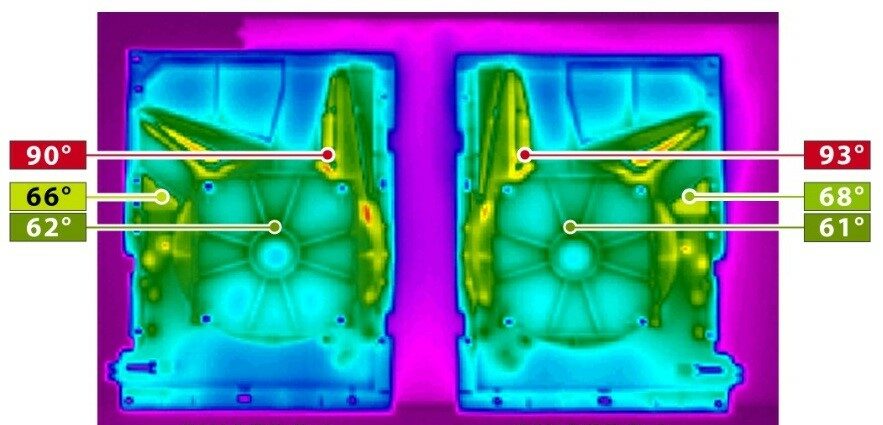
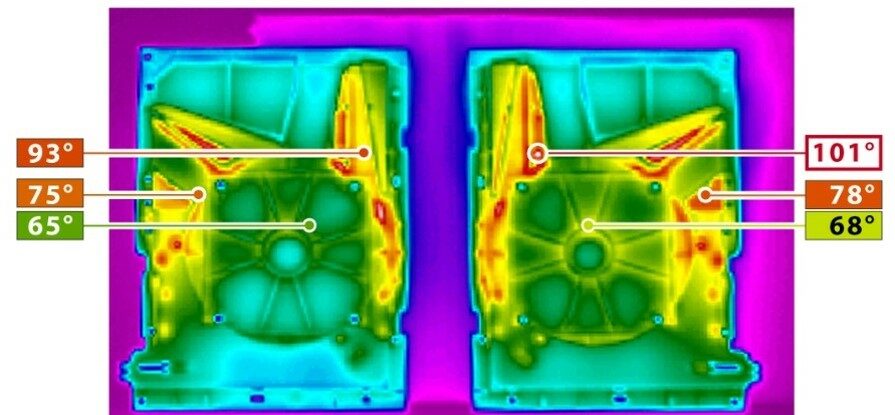
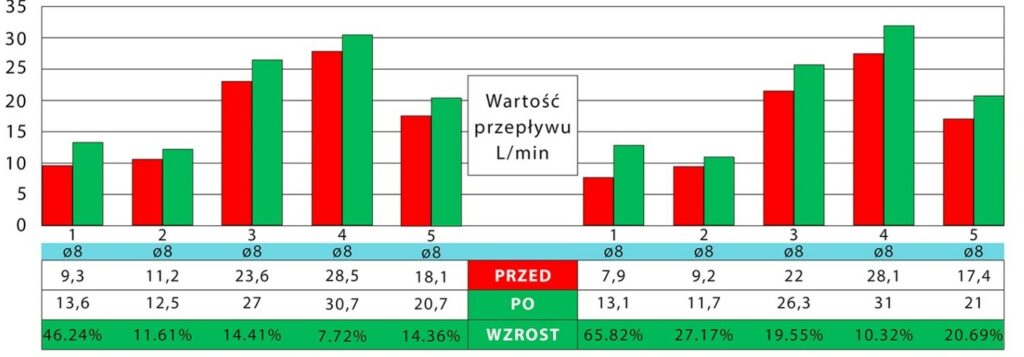
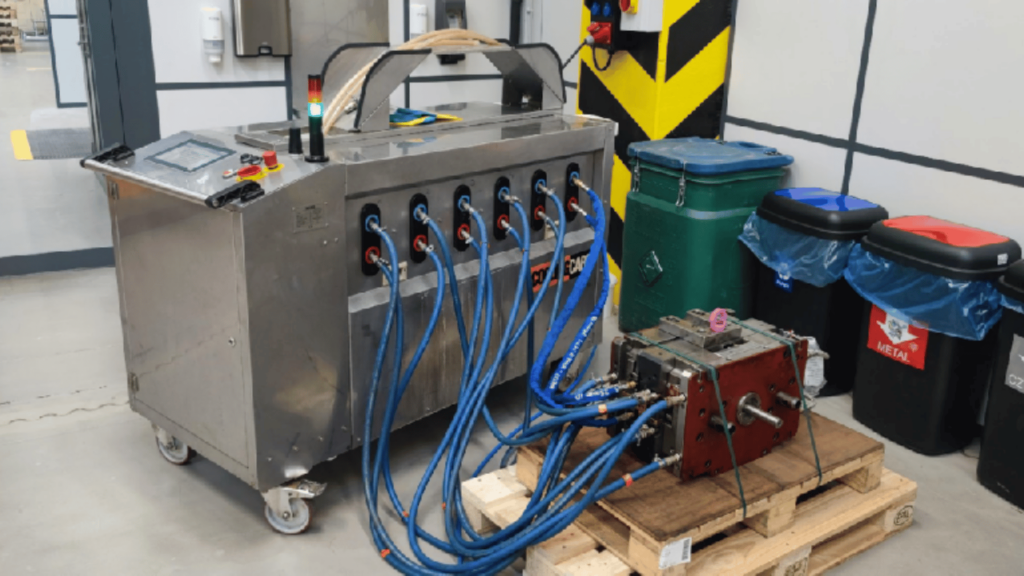
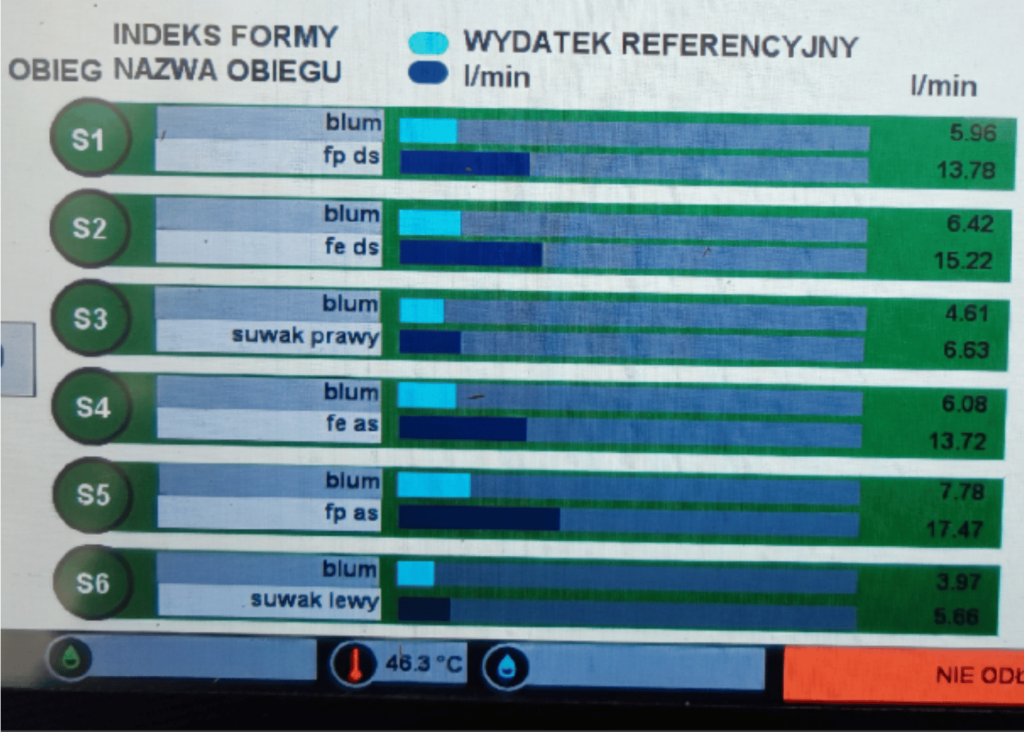