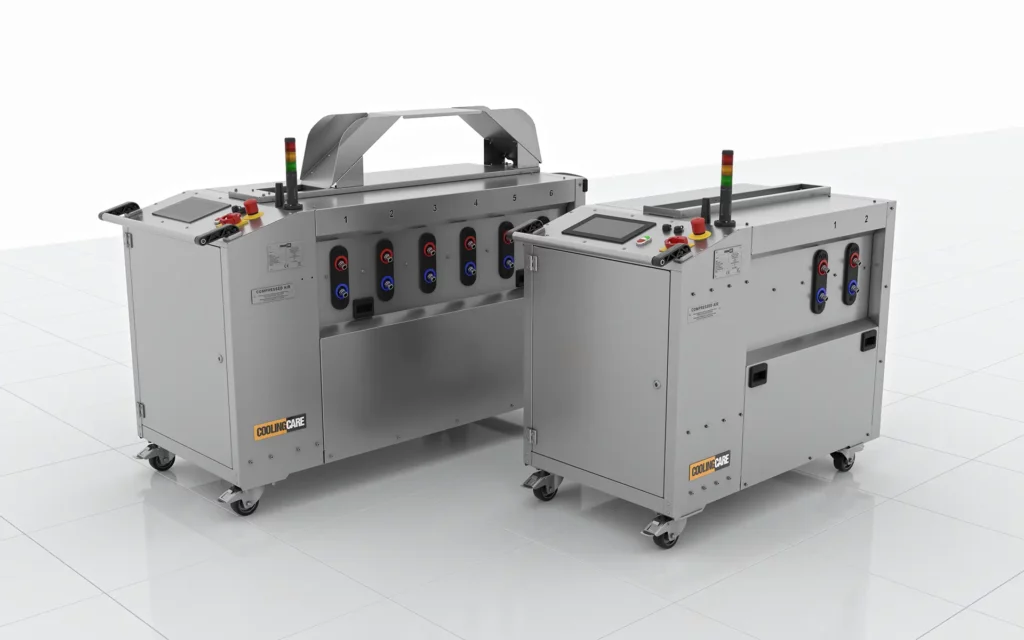
CA series
CA series devices are the most advanced systems in the CoolingCare family. These fully automated machines have been designed to meet the highest demands in the modern plastics production environment.
They are packed with features that allow users to monitor and maintain full control of the cooling performance of their molds.
They are equipped with features that allow users to monitor and maintain full control over the cooling performance of their molds.
The most important features of this series:
Feature | Function | Benefit |
---|---|---|
A patented, hydromechanical cleaning method using the cavitation effect | Shorter cleaning time, cleaning agents only used to soften the stone | Less risk of mold damage, more molds cleaned in the same time |
Six independent cleaning sections with a dedicated feed pump and cavitation generator | Higher cleaning efficiency, more channels cleaned simultaneously, no need to bridge channels | More molds cleaned at the same time, higher cost-performance ratio |
Smart cleaning modes | The channels are cleaned only as long as necessary | Reduced risk of mold damage, optimized machine performance |
Fully automated process, built-in algorithms including leak tests, flow measurements and cleaning | There is no need to manually switch between functions | Lower operating costs, personnel are only required to connect the mold and start the process |
Precise real-time liquid level monitoring with ultrasonic probe | Leak/overfill protection with configurable alarm trigger values | Reducing the risk of mold damage in the event of a sudden leak |
CA-6
Six-circuit system
CA-2
Two-circuit system
Would you like to know more?
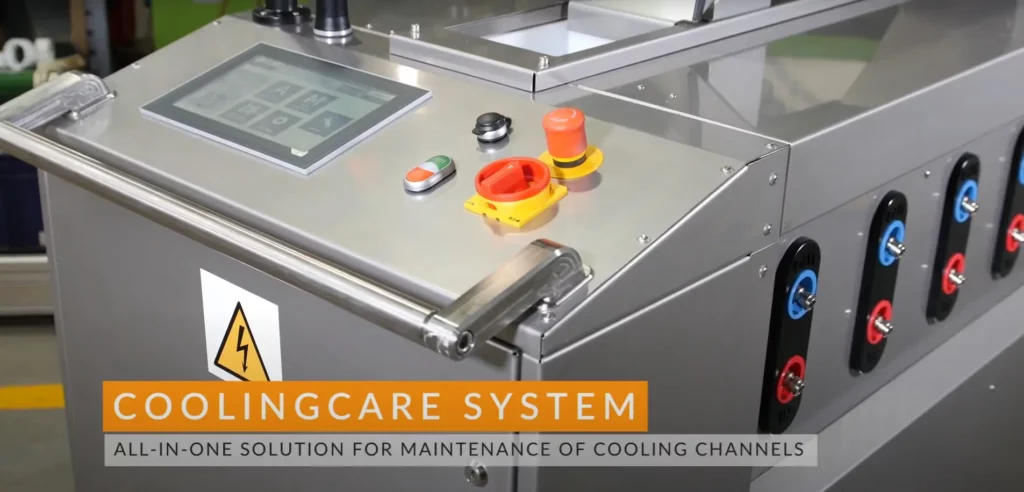
Detailed information
Functionality
Cleaning
Hybrid hydro-mechanical cleaning process based on cavitation
A patented cleaning method that uses the cavitation phenomenon to increase cleaning efficiency. The high dynamics of the cleaning process allows for the mechanical removal of scale deposits, while the cleaning medium solution is only intended to soften the contaminants adhering to the channel surface. This solution brings many benefits. The channels are cleaned for much less time, which minimizes the contact time of the tool with the cleaning agent. Additionally, we can use agents with lower concentrations, which also lowers the risk of damaging the mold in the event of contact of the tool with the cleaning fluid.
Autonomous cleaning mode until achieving stable target flow rates
A feature exclusive to CA machines. Thanks to their unique design, where every section is equipped with a dedicated set of feed pumps and cavitation generators, the machine can define individual cleaning time per every channel based on the cleaning results. These can be compared to the reference flow previously saved in the database. Once the current measurement matches the one saved in the database, the cleaning process for that section ends. Every channel might reach the desired flow in different time, this is why having individual pumps per every section is crucial to enable that feature.
The machine, operating in automatic mode, itself compares the current results with the reference flow previously stored in the database. When the current measurement is a percentage close, the cleaning process for that section will end. Each channel can reach the desired flow at different times, so having separate pumps in each section is key to enabling this function. The set % to be achieved can be individually determined by the operator.
Cleaning time of each channel is defined independently. The process lasts as long as necessary
A feature exclusive to CA machines. Thanks to their unique design, where every section is equipped with a dedicated set of feed pumps and cavitation generators, the machine can define individual cleaning time per every channel based on the cleaning results. These can be compared to the reference flow previously saved in the database. Once the current measurement matches the one saved in the database, the cleaning process for that section ends. Every channel might reach the desired flow in different time, this is why having individual pumps per every section is crucial to enable that feature.
Drying of the channel after cleaning
CA series machines automatically dry the channels after any liquid operation is completed. This allows us to minimize leakage when disconnecting the hoses. Other models require the operator to perform the blowing operation manually
Export of mold cleaning results is available
When the operation is completed, the machine displays a report that can be exported to an external device. CA machines have a built-in database with the history of all operations performed for each of the saved projects to which we have access from the controller. CS devices only keep records of the last project, and creating a new one overwrites the previous one. However, it is possible to download historical results for all projects to a mobile device via hotspot.
Logging of mold cleaning history in the machine's database
A key function for all companies that want to monitor the cooling efficiency of molds throughout their operation. In this way, they can pursue a 'preventive maintenance' policy and clean the channels only when a decrease in expenditure is recorded compared to those recorded in the database. CA series devices additionally have automatic cleaning algorithms that are directly linked to historical expenses recorded in the database, which further facilitates the operator's work.
Diagnostics
Leakage and blockage test using compressed air
Pressure and patency tests allow for a preliminary assessment of the condition of the channel as well as verification of the correct connection of the machine to the mold. A properly performed leak test also allows for the detection of inter-channel leaks inside the mold. If the channel is leaking, an attempt to clean it will lead to even greater leakage and spillage of the cleaning media onto the molding elements, which may lead to damage to the mold. Detecting a blockage may suggest improper connection of the circuits or actual clogging, which requires cleaning procedures other than conventional washing.
Automatic diagnostics with automatic switching to cleaning mode
The operator can start the machine in automatic mode, where after performing diagnostic operations, the machine will start the cleaning process itself in accordance with a previously defined work algorithm.
The machine, operating in automatic mode, itself compares the current results with the reference flow previously stored in the database. When the current measurement is a percentage close, the cleaning process for that section will end. Each channel can reach the desired flow at different times, so having separate pumps in each section is key to enabling this function. The set % to be achieved can be individually determined by the operator.
Flow rate measurement with the ability to compare to target flow rates saved in the database
The machine allows you to compare the current flow rate with the historical record in the database and then autonomously decide to continue the process or end it depending on the results obtained. The operator can define the % of the reference flow that the machine should strive for.
Drying of the channels with compressed air after the diagnostic check
every liquid-based operation needs to be followed by an airblow in order to remove the liquid and dry the channels. CA machines automatically end cleaning & diagnostics operations with airblow to ensure no liquid is left in the channels. In the case of other machines airblow must be done manually by the operator, performing a sequence of actions given in the manual or presented to him in the PLC screen
Maintenance
Flushing the channels with mains water
rinsing channels after the cleaning process is required to flush the cleaning agent residues from the channels. This can be either done by external water supply input, or by means of a second tank with water mixed with corrosion inhibitors. If there is no external water supply connection available, the operator needs to replace the water in the second tank on a regular basis, as its pH value will drop with each rinsing. This will make the water acidic, and therefore inapropriate for neutralization of channels.
Option for additional protection of channels with a corrosion inhibitor
rinsing channels after the cleaning process is required to flush the cleaning agent residues from the channels. This can be either done by external water supply input, or by means of a second tank with water mixed with corrosion inhibitors. If there is no external water supply connection available, the operator needs to replace the water in the second tank on a regular basis, as its pH value will drop with each rinsing. This will make the water acidic, and therefore inapropriate for neutralization of channels.
The machine, operating in automatic mode, itself compares the current results with the reference flow previously stored in the database. When the current measurement is a percentage close, the cleaning process for that section will end. Each channel can reach the desired flow at different times, so having separate pumps in each section is key to enabling this function. The set % to be achieved can be individually determined by the operator.
Additional features
Tank filling and emptying function
thanks to the use of an ultrasonic probe in CA and CS machines, we can precisely, automatically fill the tanks. Thanks to this, we always have the same amount of liquid in the tank, which allows us to prepare the exact concentration of the cleaning solution. When filling manually, the amount in the liquid in the tank may vary.
Clogged suction filter sensors
allows you to monitor the degree of filter clogging in real time. The machine itself informs the operator about the need to clean them, so he does not have to guess when it is time to clean them.
Ability to modify operating parameters and algorithms
The user can modify all operating parameters of the device and can also activate or deactivate individual functions in automatic mode.
Recording of operating hours for individual pumps and pulsators
allows you to assess the degree of wear of pump components (often machine sections are not used equally often)
Monitoring of operating hours for the cleaning medium
allows you to assess how often the cleaning medium should be used without having to measure the pH of the solution every time.
Remote software update
allows you to connect to the device via the Internet and remotely upload the software without the need to visit the plant
Ability to create user accounts with different levels of access to machine functions
allows you to limit the distance to modify machine parameters for people who have not been trained in the operation of the device
Language selection
ability to switch between English, German, Spanish, French, Italian and Polish
Compressed air source capacity control
If the pressure during machine operation drops below the required pressure (4 bar), the machine will turn off the heating. If the air flow drops during the blow-through function, the machine waits until the pressure in the system increases and continues blowing until the set blow-through time expires.
Measurement of pH and conductivity of the cleaning medium Export to Sheets
measuring tools dedicated to the machine allow you to assess the level of use of the cleaning medium
Safety
System of sensors and algorithms ensuring stable and safe operation
- blow-through algorithm (ramp) - protects the compartment with a sudden pressure drop, the pressure increases gradually, thus minimizing the risk of damage to the partitions and other elements of the cooling system
- algorithm for verifying the correct reading from all pressure sensors - allows verification of the presence of residual pressure in the system, thus eliminating the possibility of liquid flowing back into the pneumatic system when the valve position is changed
- the machine informs the operator about the presence of residual pressure in the system, so he can release it manually and safely disconnect the hoses
- Each valve has a position control sensor - thanks to this function, the operator cannot start the machine in an incorrect configuration
- Algorithm for identifying the problem of circulation blockage if the operator misses the patency test - if the flow rate during diagnostics is very low, the machine will inform the operator about the potential blockage and exclude a given section in automatic mode. If the canal is blocked, they should be cleaned individually in manual mode.
Monitoring of cleaning medium leakage during cleaning
Ultrasonic probe in the cleaning tank allows for precise, real-time measurement of liquid level. The operator can define an allowable volume drop not causing an alarm. This can be as low as 10mm (an equivalent of approx.1L of liquid). If the level of liquid in the tank drops by thsi value, the machine will automatically stop the process and send a text message to the operator informing him about a possible leakage.
Tank solution level monitoring
it can be a precise measurement (ultrasonic probe measuring the exact amount of liquid) or floater-based measurement, which gives a rough estimation
Tank solution temperature monitoring
temperature sensors (one in the heater, the other on the filter housing)
Heating element damage control
the machine is protected by a thermostat placed on the heating element and a software protection that disconnects the heating if the permissible temperature is exceeded.
Faulty phase connection control
the machine detects the absence of any of the phases or the incorrect order of their connection, this prevents damage to the centrifugal pump
Control of medium flow continuity through the heating system
The flow heating system is connected to a dedicated membrane pump that forces the circulation of liquid through the tank in which the heater is placed. The algorithm verifies whether the heating element is fully immersed in the liquid and whether the liquid flow rate is appropriate.
The machine, operating in automatic mode, itself compares the current results with the reference flow previously stored in the database. When the current measurement is a percentage close, the cleaning process for that section will end. Each channel can reach the desired flow at different times, so having separate pumps in each section is key to enabling this function. The set % to be achieved can be individually determined by the operator.
Pneumatic system humidity sensor Export to Sheets
if the presence of water is detected in the compressed air, the machine will block further operation. This is to protect the pneumatic system of the machine, which is the most sensitive element of the entire structure.
Service
- Modular design allowing for easy replacement of components
- Ability to remotely assess the cause of device failure at the customer's location
- Evaluation of the correct operation of filter clogging sensors
Technical data
CA-6
Number of cleaning sections | 6 |
Base medium | Water |
Permitted cleaning agent | Depending on the type of deposit (DS1, DS2) |
Diagnostic medium | Water + corrosion inhibitor (optional) |
Diagnostic pump type | Rotary |
Cleaning medium supply pump type | Membrane (x4) |
Pulsator type | Membrane (x6) |
Maximum diagnostic pump capacity | 73L/min |
Cleaning medium pump capacity | 15L/min |
Required air pressure | 8 Bar |
Air consumption | 750L/min |
Cleaning fluid tank capacity | 100L |
Diagnostic fluid tank capacity | 55L |
Maximum cleaning fluid temperature | 50˚C |
Hydraulic hose connection type | 12x G1/2" |
Mains water connection type | 1x G1/2″, 1x G3/4″ |
Compressed air connection type | Standard EURO profile series 26 RQS |
Control panel | Controller with 10.1" touch panel |
Device weight (without fluids) | 415kg |
Maximum sound level | 83dB |
--Installed power | 3 kW (1 heater) |
Supply voltage | 400 VAC (three-phase) |
Current consumption | 13A |
CA-2
Number of cleaning sections | 2 |
Base medium | Water |
Permitted cleaning agent | Depending on the type of deposit (DS1, DS2) |
Diagnostic medium | Water + corrosion inhibitor (optional) |
Diagnostic pump type | Rotary |
Cleaning medium supply pump type | Membrane (x2) |
Pulsator type | Membrane (x2) |
Maximum diagnostic pump capacity | 73L/min |
Cleaning medium pump capacity | 15L/min |
Required air pressure | 8 Bar |
Air consumption | 380L/min |
Cleaning fluid tank capacity | 100L |
Diagnostic fluid tank capacity | 55L |
Maximum cleaning fluid temperature | 50˚C |
Hydraulic hose connection type | 4x G1/2" |
Mains water connection type | 1x G1/2″, 1x G3/4″ |
Compressed air connection type | Standard EURO profile series 26 RQS |
Control panel | Controller with 10.1" touch panel |
Device weight (without fluids) | 275kg |
Maximum sound level | 75dB |
Installed power | 3 kW (1 heater) |
Supply voltage | 400 VAC (three-phase) |
Current consumption | 10A |
Machine measurements
CA-6
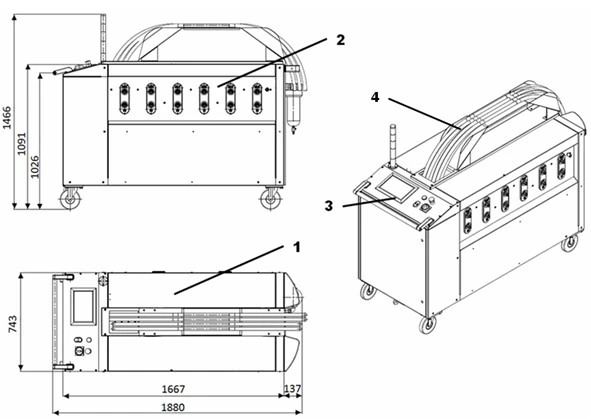
1 - tank section, 2 - mold connection section, 3 - control section, 4 - hydraulic hose container
CA-2
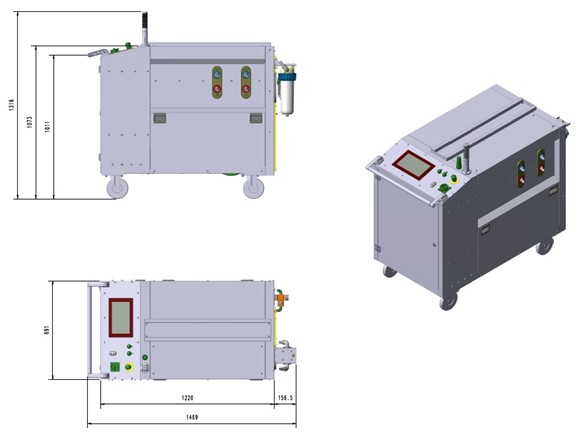
1 - tank section, 2 - mold connection section, 3 - control section

CM series
The CM series of machines are universal, configurable units that can be equipped with virtually all necessary functions according to the user's needs.
The proposed capacities of pumps and cavitation generators allow you to choose the optimal device adapted to the size of the molds and the system of collectors connecting the cooling channels. Additionally, chemical tanks can be equipped with 6kW heaters, and cleaning takes place in two directions, which significantly speeds up the process.
The most important features of this series:
Feature | Function | Benefit |
---|---|---|
Intuitive interface with built-in tutorial | The operator is informed step by step what sequence of operations he should perform to start the given process | The machine is easy to use, quick implementation time for the operator |
Automatic change of flow direction triggered from the desktop | Higher efficiency and uniformity of the cleaning process, no need to reconnect hoses manually | The channels are equally clean on each side, regardless of their length, with less involvement on the part of the operator |
Diaphragm pump equipped with fiber optic sensors measuring the number of diaphragm deflections over time | Real-time flow measurement function during cleaning | The entire operation time is shorter, there is no risk of mixing liquids |
Optional section 7 with cavitation generator | Possibility of using the cavitation phenomenon when cleaning heavily contaminated circuits | Higher cleaning dynamics and efficiency, shorter operation time |
Flow heating module with a power of 6kW | No heating elements in the tank, higher cleaning efficiency thanks to increased temperature | Easy access to the bottom of the tank, the operator has no contact with the heating element, shorter cleaning time |
CME-7 / CME-5
Six-circuit system (with an optional seventh, additional CAVI circuit)
CMS
Expansion modulefor CM series machines
CS series
The CS2 machine is the smallest in the series intended for users with the highest demands. It is equipped with all the necessary functions known from flagship CA machines, apart from the mold database and the ability to communicate via OPC UA.
CS2 is produced only in a two-circuit version with a semi-automatic operating mode. Intuitive and user-friendly software allows for very quick implementation of staff and starting work without preliminary training.
The most important features of this series:
Feature | Function | Benefit |
---|---|---|
A patented, hydromechanical cleaning method using the cavitation effect | Shorter cleaning time, cleaning agents only used to soften the stone | Less risk of mold damage, more molds cleaned in the same time |
Two independent cleaning sections with a dedicated feed pump and cavitation generator | Higher cleaning efficiency, more channels cleaned simultaneously, no need to bridge channels | More molds cleaned at the same time, higher cost-performance ratio |
Reversal of the flow direction of the cleaning medium | Even cleaning dynamics on both sides of the channel | Greater cleaning efficiency when connecting channels in series |
Built-in tutorial mode, easy-to-use interface | Operators simply follow the instructions displayed on the PLC screen | Fast learning curve for operators, low risk of making mistakes when setting up the machine |
Precise real-time liquid level monitoring with ultrasonic probe | Leak/overfill protection with configurable alarm trigger values | Reducing the risk of mold damage in the event of a sudden leak |
CS-2
Two-circuit semi-automatic system
Detailed information
Functionality
Cleaning
Hydromechanical, hybrid cleaning process based on the cavitation phenomenon
A patented cleaning method that uses the cavitation phenomenon to increase cleaning efficiency. The high dynamics of the cleaning process allows for the mechanical removal of scale deposits, while the cleaning medium solution is only intended to soften the contaminants adhering to the channel surface. This solution brings many benefits. The channels are cleaned for much less time, which minimizes the contact time of the tool with the cleaning agent. Additionally, we can use agents with lower concentrations, which also lowers the risk of damaging the mold in the event of contact of the tool with the cleaning fluid.
Flow reversal
Flow reversal can be useful if the operator decides to bridge multiple channels and connect them to a single cleaning section. In such a case flow reversal can minimize the risk of uneven cleaning process
Channel airblow after cleaning
Airblow must be done manually by the operator, performing a sequence of actions given in the manual or presented to him in the PLC screen
Record of mold cleaning history in the machine's database
CS devices only keep records of the last project, and creating a new one overwrites the previous one. However, it is possible to download historical results for all projects to a mobile device via hotspot.
Diagnostics
Pressure test for leakage identification
Pressure and patency tests allow for a preliminary assessment of the condition of the channel as well as verification of the correct connection of the machine to the mold. A properly performed leak test also allows for the detection of inter-channel leaks inside the mold. If the channel is leaking, an attempt to clean it will lead to even greater leakage and spillage of the cleaning media onto the molding elements, which may lead to damage to the mold. Detecting a blockage may suggest improper connection of the circuits or actual clogging, which requires cleaning procedures other than conventional washing.
Drying channels with compressed air after diagnostics
Every liquid-based operation needs to be followed by an airblow in order to remove the liquid and dry the channels. CA machines automatically end cleaning & diagnostics operations with airblow to ensure no liquid is left in the channels. In the case of other machines airblow must be done manually by the operator, performing a sequence of actions given in the manual or presented to him in the PLC screen
Postprocess operations
Channel rinsing with external water supply
Rinsing channels after the cleaning process is required to flush the cleaning agent residues from the channels. This can be either done by external water supply input, or by means of a second tank with water mixed with corrosion inhibitors. If there is no external water supply connection available, the operator needs to replace the water in the second tank on a regular basis, as its pH value will drop with each rinsing. This will make the water acidic, and therefore inapropriate for neutralization of channels.
Neutralization of cleaning agent residues in the channels after cleaning
Rinsing channels after the cleaning process is required to flush the cleaning agent residues from the channels. This can be either done by external water supply input, or by means of a second tank with water mixed with corrosion inhibitors. If there is no external water supply connection available, the operator needs to replace the water in the second tank on a regular basis, as its pH value will drop with each rinsing. This will make the water acidic, and therefore inapropriate for neutralization of channels.
Possibility of additional protection of channels with a corrosion inhibitor
Rinsing channels after the cleaning process is required to flush the cleaning agent residues from the channels. This can be either done by external water supply input, or by means of a second tank with water mixed with corrosion inhibitors. If there is no external water supply connection available, the operator needs to replace the water in the second tank on a regular basis, as its pH value will drop with each rinsing. This will make the water acidic, and therefore inapropriate for neutralization of channels.
The machine, operating in automatic mode, itself compares the current results with the reference flow previously stored in the database. When the current measurement is a percentage close, the cleaning process for that section will end. Each channel can reach the desired flow at different times, so having separate pumps in each section is key to enabling this function. The set % to be achieved can be individually determined by the operator.
Additional functions
Tank filling and emptying
Thanks to the use of an ultrasonic probe in the main cleaning media tank (CA and CS machines only) the machine will know exactly how much water is required to fill-in the tank. This feature allows to have repeatable concentration of cleaning solution prepared.
Monitoring of suction filter clogging level
Allows you to monitor the degree of filter clogging in real time. The machine itself informs the operator about the need to clean them, so he does not have to guess when it is time to clean them.
Calibration of parameters and work algorithms
The user can modify all operating parameters of the device and can also activate or deactivate individual functions in automatic mode.
Software available in different language versions
Ability to switch between English, German, Spanish, French, Italian and Polish
Measurement of pH and conductivity of the cleaning solution
Measuring tools dedicated to the machine allow you to assess the level of use of the cleaning medium
Safety
A set of sensors and algorithms ensuring stable and safe operation
- Blow-through algorithm (ramp) - protects the compartment with a sudden pressure drop, the pressure increases gradually, thus minimizing the risk of damage to the partitions and other elements of the cooling system
- Algorithm for verifying the correct reading from all pressure sensors - allows verification of the presence of residual pressure in the system, thus eliminating the possibility of liquid flowing back into the pneumatic system when the valve position is changed
- The machine informs the operator about the presence of residual pressure in the system, so he can release it manually and safely disconnect the hoses
- Each valve has a position control sensor - thanks to this function, the operator cannot start the machine in an incorrect configuration
- Algorithm for identifying the problem of circulation blockage if the operator misses the patency test - if the flow rate during diagnostics is very low, the machine will inform the operator about the potential blockage and exclude a given section in automatic mode. If the canal is blocked, they should be cleaned individually in manual mode.
Leakage detection system
Ultrasonic probe in the cleaning tank allows for precise, real-time measurement of liquid level. The operator can define an allowable volume drop not causing an alarm. This can be as low as 10mm (an equivalent of approx.1L of liquid). If the level of liquid in the tank drops by thsi value, the machine will automatically stop the process and send a text message to the operator informing him about a possible leakage.
Liquid level measurement in the tank
It can be a precise measurement (ultrasonic probe measuring the exact amount of liquid) or floater-based measurement, which gives a rough estimation
Liquid temperature control combined with automatic heater activation/deactivation
Temperature sensors (one in the heater, the other on the filter housing)
Heating element damage control
The machine is protected by a thermostat placed on the heating element and a software protection that disconnects the heating if the permissible temperature is exceeded.
Identification of faulty phase connection
The machine detects the absence of any of the phases or the incorrect order of their connection, this prevents damage to the centrifugal pump
Control of the continuity of the liquid flow through the heater system
The flow heating system is connected to a dedicated diaphragm pump that forces the circulation of liquid through the tank in which the heater is placed. The algorithm verifies whether the heating element is fully immersed in the liquid and whether the liquid flow rate is appropriate.
The machine, operating in automatic mode, itself compares the current results with the reference flow previously stored in the database. When the current measurement is a percentage close, the cleaning process for that section will end. Each channel can reach the desired flow at different times, so having separate pumps in each section is key to enabling this function. The set % to be achieved can be individually determined by the operator.
Moisture detection in pneumatic system
if the presence of water is detected in the compressed air, the machine will block further operation. This is to protect the pneumatic system of the machine, which is the most sensitive element of the entire structure.
Service
- Modular design allowing easy replacement of components
Technical data
Function | Value |
---|---|
Operating mode | semi-automatic |
Power supply | 3x400V AC |
Control/touch screen | 7" |
Number of circuits | 28 |
Cleaning medium tank | 0L |
Diagnostic medium tank | 25L |
Membrane pumps (L/min) | 252x25 |
Cavitation generator (L/min) | 6kW |
Flow heater | yes |
Suction filter | yes |
Return filter | yes |
CLEANING | |
Hydromechanical hybrid cleaning process based on the cavitation phenomenon | yes |
Cleaning process based on single-state, pulsating supply of cleaning liquid to the system | - |
Change of flow direction | yes |
Autonomous cleaning mode until stable reference flow rates are reached | - |
The cleaning time of each channel is defined independently. The process lasts as long as necessary. | - |
Channel drying after cleaning | manual |
DIAGNOSTICS | |
Possible export of mold cleaning results | yes |
Saving the history of mold cleaning in the machine database | - |
Modular design allowing for easy replacement of components | yes |
Leakage test using compressed air | yes |
Patency test using compressed air | - |
Automatic diagnostics with unattended transition to cleaning mode | - |
Flow rate measurement with the possibility of referring to reference flow rates stored in the database | - |
Real-time flow rate measurement | yes |
MAINTENANCE | |
Drying channels with compressed air after diagnostics | yes |
Flushing channels with mains water | yes |
Neutralization of cleaning agent residues in channels after cleaning | yes |
ADDITIONAL FUNCTIONS | |
Possibility of additional protection of channels with corrosion inhibitor | yes |
Function of filling and emptying tanks | yes |
Modular design allowing for easy replacement of components | - |
Suction filter clogging sensors | yes |
Possibility of calibrating parameters and operating algorithms | yes |
Recording the number of operating hours for individual pumps and pulsators | - |
Monitoring the number of operating hours for the cleaning medium | - |
Remote software update | yes |
Possibility to create user accounts with different levels of access to machine functions | yes |
Choice of language version | yes |
SAFETY | |
Built-in drain valve for emergency emptying of tanks | manual |
Compressed air source capacity control | no |
Measurement of pH and conductivity of the cleaning medium | yes |
OPC UA module | yes |
System of sensors and algorithms ensuring stable and safe operation | yes |
Monitoring of cleaning medium leakage during cleaning | yes |
Control of the solution level in the tank | yes |
Control of the solution temperature in the tank | yes |
Checking for damage to heating elements | - |
SERVICE | |
Checking for incorrect phase connection | yes |
Checking the continuity of medium flow through the heating system | yes |
Additional protection against tank damage and leakage | - |
Pneumatic system humidity sensor | yes |
Modular design allowing for easy replacement of components | yes |
Possibility of remote assessment of the cause of device failure at the customer's location | - |
Evaluation of the correct operation of filter clogging sensors | yes |
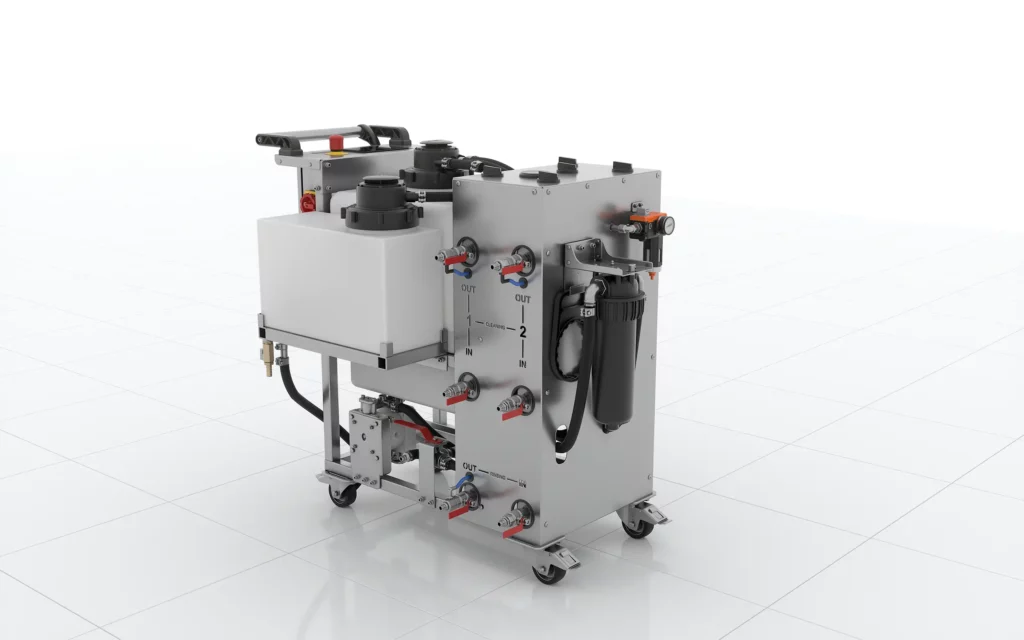
CP series
CP series - compact, affordable devices. Perfect for production plants with few molds. CP devices are based on the same cleaning technology as the higher-end CoolingCare models.
CP-2 DUO
Two-circuit system with an additional tank for rinsing the channels after cleaning
CP-1
Single-circuit system equipped
with a tank and a compact cleaning module
CP CASE
Single-circuit, compact cleaning module without tank