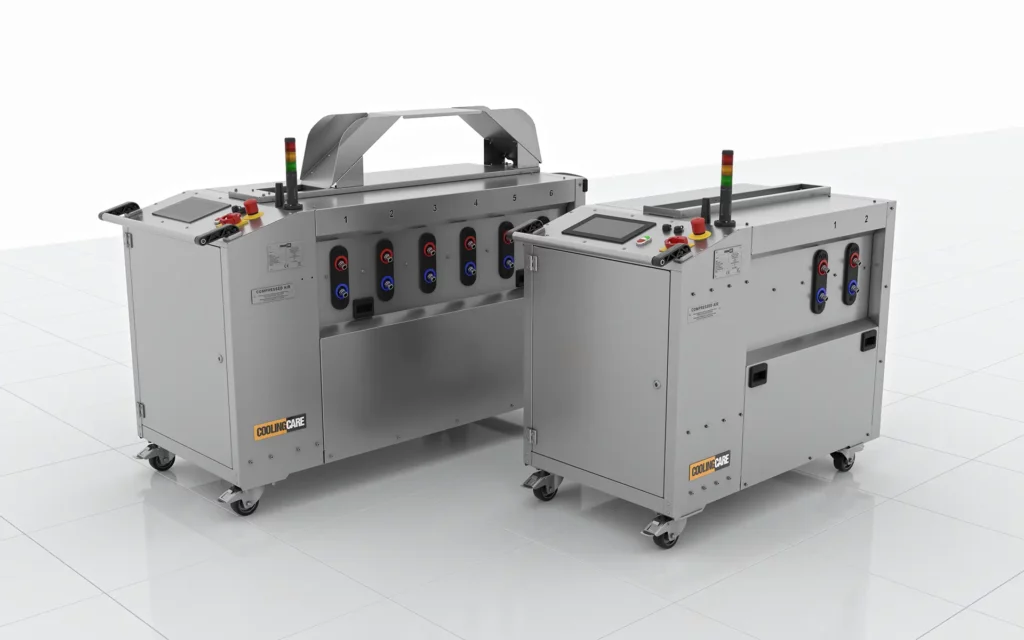
CA series
The CA series machines are the most advanced systems in the CoolingCare family. These fully automated machines are designed to meet the highest requirements in the modern plastics production environment.
They are equipped with features that allow users to monitor and maintain full control over the cooling performance of their molds.
Highlights of the series:
Feature | Function | Benefit |
---|---|---|
Patented hydromechanical cleaning method using cavitation effect | Shorter cleaning time, cleaning agents used only to soften scale | Less risk of mold damage, more molds cleaned at the same time |
Six independent cleaning sections with dedicated feed pump and cavitation generator | Higher cleaning efficiency, more channels cleaned simultaneously, no bridging of channels required | More molds cleaned in the same time, higher cost/performance ratio |
Intelligent cleaning modes | The channels are cleaned only as long as necessary | Less risk of mold damage, optimized machine performance |
Automated process, built-in algorithms including leak testing, flow measurement and cleaning | No need to manually switch between functions | Lower operating costs, staff is only required to connect the mold and start the process |
Precise real-time liquid level monitoring with ultrasonic probe | Leakage / overflow protection with configurable alarm trigger values | Reducing the risk of mold damage in case of sudden leakage |
Feature
Patented hydromechanical cleaning method using cavitation effect
Six independent cleaning sections with dedicated feed pump and cavitation generator
Intelligent cleaning modes
Automated process, built-in algorithms including leak testing, flow measurement and cleaning
Precise real-time liquid level monitoring with ultrasonic probe
Function
Shorter cleaning time, cleaning agents used only to soften scale
Higher cleaning efficiency, more channels cleaned simultaneously, no bridging of channels required
The channels are cleaned only as long as necessary
No need to manually switch between functions
Leakage / overflow protection with configurable alarm trigger values
Benefit
Less risk of mold damage, more molds cleaned at the same time
More molds cleaned in the same time, higher cost/performance ratio
Less risk of mold damage, optimized machine performance
Lower operating costs, staff is only required to connect the mold and start the process
Reducing the risk of mold damage in case of sudden leakage
CA-6
Six-speed system
CA-2
Two-speed system
Would you like to learn more?
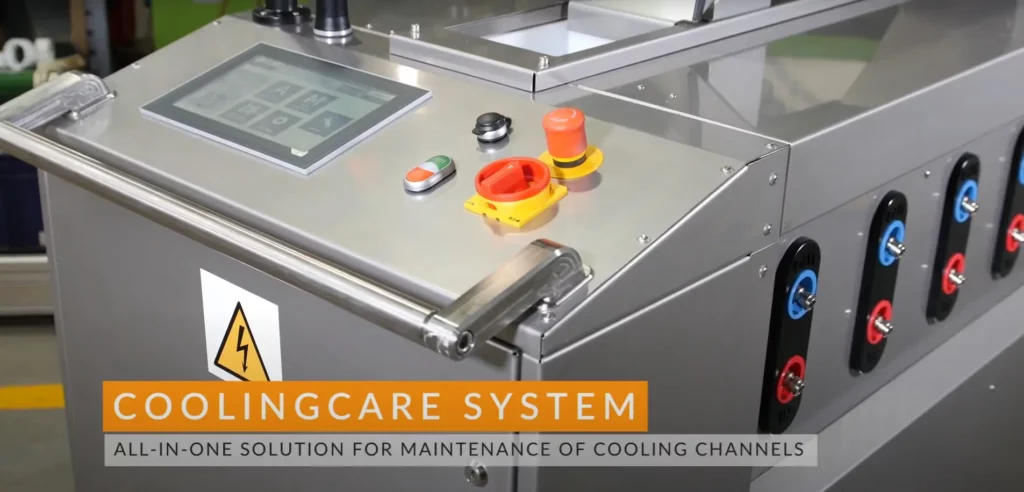
Detailed information
Functionality
Cleaning
Hydromechanical hybrid cleaning process based on the phenomenon of cavitation
A patented cleaning method that uses the phenomenon of cavitation to increase cleaning efficiency. The high dynamics of the cleaning process allows the mechanical removal of scale deposits, while the cleaning medium solution only aims to soften the contaminants adhering to the surface of the channel. Such a solution has many advantages. The channels are cleaned for a much shorter period of time, thus minimizing the contact time between the tool and the cleaning medium. In addition, we can use agents of lower concentration, which also minimizes the risk of damage to the mold in case of contact between the tool and the cleaning fluid.
Autonomous cleaning mode until stable reference expenditures are reached
Thanks to a unique design in which each section is equipped with a dedicated set of feeding pumps and cavitation generators, the machine can define an individual cleaning time for each channel based on historical flow expenses or stabilization of current expenses.
The machine, operating in automatic mode, itself compares the current results with the reference flow previously stored in the database. When the current measurement is a percentage close, the cleaning process for that section will end. Each channel can reach the desired flow at different times, so having separate pumps in each section is key to enabling this function. The set % to be achieved can be individually determined by the operator.
The cleaning time for each channel is defined independently. The process takes as long as necessary
Thanks to a unique design in which each section is equipped with a dedicated set of feeding pumps and cavitation generators, the machine can define an individual cleaning time for each channel based on historical flow expenses or stabilization of current expenses.
Drying the channel after cleaning
CA series machines automatically dry the channels after any of the liquid operations are completed. This allows us to minimize leakage when the hoses are disconnected. Other models require the operator to perform the purging operation manually
Possible export of mold cleaning results
When the operation is completed, the machine displays a report that can be exported to an external device. CA machines have a built-in database with a history of all operations performed for each saved project, which we can access from the controller.
Record of mold cleaning history in the machine database
A key feature for all companies that want to monitor the cooling performance of their molds over their entire life cycle.In this way they can carry out a policy of 'preventive maintenace' and clean the ducts only when a decrease in spending is recorded against those stored in the database. The CA series devices additionally have cleaning algorithms in automatic mode that are directly coupled to the historical expenditures stored in the database, which further facilitates the operator's work.
Diagnostics
Leakage and patency test using compressed air
Leakage and patency tests allow a preliminary assessment of the condition of the channel as well as verification of the correct connection of the machine to the mold. A properly performed leak test also allows the detection of inter-channel leakage inside the mold. In a situation where the channel is leaking, a cleaning attempt will lead to even more leakage and cleaning medium spilling onto the molding parts, which can lead to mold damage. Detection of an obstruction may suggest improperly plugged circuits or actual clogging, which requires cleaning procedures other than conventional washing.
Automatic diagnostics with maintenance-free transition to cleaning mode
The operator can run the machine in automatic mode, where, after diagnostic operations, the machine itself will start the cleaning process according to a predefined work algorithm.
The machine, operating in automatic mode, itself compares the current results with the reference flow previously stored in the database. When the current measurement is a percentage close, the cleaning process for that section will end. Each channel can reach the desired flow at different times, so having separate pumps in each section is key to enabling this function. The set % to be achieved can be individually determined by the operator.
Measurement of flow expenditure with the possibility of reference to reference expenditures stored in the database
The machine allows the current flow rate to be compared with the historical record in the database, and then autonomously decide whether to continue the process or terminate it depending on the results. The operator can define a % reference flow rate for the machine to aim for.
Drying the ducts with compressed air after the diagnostics are completed
Each liquid-based operation must be followed by an air purge to remove the liquid and dry the channels. CA series machines automatically terminate cleaning and diagnostic operations with an air purge to ensure that no liquid remains in the ducts. On other machines, blowing must be done manually by the operator, following a sequence of steps given in the manual or shown to him on the PLC screen
Maintenance
Flushing the sewers with mains water
A patented cleaning method that uses the phenomenon of cavitation to increase cleaning efficiency. The high dynamics of the cleaning process allows the mechanical removal of scale deposits, while the cleaning medium solution only aims to soften the contaminants adhering to the surface of the channel. Such a solution has many advantages. The channels are cleaned for a much shorter period of time, thus minimizing the contact time between the tool and the cleaning medium. In addition, we can use agents of lower concentration, which also minimizes the risk of damage to the mold in case of contact between the tool and the cleaning fluid.
Possibility of additional protection of channels with corrosion inhibitor
Thanks to a unique design in which each section is equipped with a dedicated set of feeding pumps and cavitation generators, the machine can define an individual cleaning time for each channel based on historical flow expenses or stabilization of current expenses.
The machine, operating in automatic mode, itself compares the current results with the reference flow previously stored in the database. When the current measurement is a percentage close, the cleaning process for that section will end. Each channel can reach the desired flow at different times, so having separate pumps in each section is key to enabling this function. The set % to be achieved can be individually determined by the operator.
Additional features
Tank filling and emptying function
Thanks to the use of an ultrasonic probe in CA and CS machines, we have the possibility of precise, automatic filling of tanks. As a result, we have the same amount of liquid in the tank each time, which allows us to prepare the exact concentration of the cleaning solution. In the case of manual filling, the amount in the liquid in the tank may vary.
Suction filter clogging sensors
It allows real-time monitoring of how clogged the filters are. The machine itself informs the operator when they need to be cleaned, so the operator doesn't have to guess when it's time to do so.
Ability to modify parameters and algorithms of operation
The user can modify all the parameters of the device's operation, and can activate lud deactivate individual functions in automatic mode.
Record of the number of operating hours for individual pumps and pulsators
It allows to assess the degree of wear of pump components (often sections of the machine are not used equally often).
Monitoring the number of operating hours for the cleaning medium
It allows to assess how often the cleaning medium should without having to measure the pH of the solution each time.
Remote software update
It allows you to connect to the device using the Internet and remotely upload software without visiting the plant.
Ability to create user accounts with different levels of access to machine functions
Allows people who are not trained in the operation of the machine to limit the distance to modify the parameters of the machine.
Choice of language version
Ability to switch between English, German, Spanish, French, Italian and Polish
Controlling the performance of the compressed air source
If the pressure drops below the required pressure (4 bars) during machine operation, the machine will disconnect heating. If the air output drops during the purge function, the machine waits until the system pressure rises and continues purging until the preset purge time expires.
Measurement of the pH and conductivity of the cleaning medium
Measuring tools dedicated to the machine make it possible to assess the level of overwork of the cleaning medium.
Security
System of sensors and algortms to ensure stable and safe operation
- Pre-blowdown algorithm (ramp) - protects the baffle from sudden pressure release, the pressure builds up gradually so that we minimize the risk of damage to the baffles and other components of the cooling system.
- Algorithm for verifying the correctness of readings from all pressure sensors - allows you to verify the presence of residual pressure in the system, which eliminates the possibility of backflow of liquid into the pneumatic system when changing the position of valves
- The machine informs the operator of the presence of residual pressure in the system, so he can drop it manually and safely unhook the hoses
- Each valve has a position control sensor - thanks to this feature, the operator has no possibility of starting the machine in the wrong configuration
- Algorithm for identifying the problem of obstruction of the circuit if the operator misses the patency test - in a situation where the flow rate is very low during the diagnostics, the machine will inform the operator of a potential obstruction and exclude the section in automatic operation mode. If there is a duct obstruction, it should be cleaned individually in manual mode.
Monitoring of cleaning fluid leakage during cleaning
An ultrasonic probe in the wash tank allows precise real-time measurement of the liquid level. The operator can define an acceptable volume drop that does not cause an alarm. It can be as low as 10 mm (equivalent to about 1 liter of liquid). If the liquid level in the tank drops by this value, the machine will automatically stop the process and send the operator an SMS message with information about a possible leak.
Controlling the level of solution in the tank
It can be a precision measurement (the ultrasonic probe measures the exact amount of liquid) or a float measurement, which gives a rough estimate.
Temperature control of the solution in the tank
Temperature sensors (one in the heater, the other on the filter housing).
Inspection of damage to heating elements
The machine has protection in the form of a thermostat located on the heating element, as well as software protection, which disconnects heating if the permissible temperature is exceeded.
Control of faulty phase connection
The machine detects the absence of any of the phases or the wrong order of their connection, this prevents damage to the impeller pump.
Control of the continuity of the medium flow through the heater system
The flow heating system is connected to a dedicated diaphragm pump that forces the fluid to circulate through the tank in which the heater is placed. An algorithm verifies that the heating element is fully immersed in the liquid and that the flow rate of that liquid is appropriate.
The machine, operating in automatic mode, itself compares the current results with the reference flow previously stored in the database. When the current measurement is a percentage close, the cleaning process for that section will end. Each channel can reach the desired flow at different times, so having separate pumps in each section is key to enabling this function. The set % to be achieved can be individually determined by the operator.
Air system moisture sensor
If the presence of water is detected in the compressed air, the machine will block the possibility of further operation. This is to protect the machine's pneumatic system, which is the most sensitive component of the entire design.
Service
- Modular design for easy component replacement
- Ability to remotely assess the cause of equipment failure at the customer's site
- Evaluation of the correct operation of the filter clogging sensors
Technical data
CA-6
number of cleaning sections | 6 |
base medium | water |
Approved cleaning agent | depending on the type of sludge (DS1, DS2) |
diagnostic agent | Water + corrosion inhibitor (optional) |
type of diagnostic pump | rotor |
type of pump supplying the cleaning medium | Membrane (x4) |
type of pulsators | Membrane (x6) |
maximum capacity of the diagnostic pump | 73L/min |
Pump capacity per cleaning medium | 15L/min |
required air pressure | 8 Bar |
air consumption | 750L/min |
cleaning fluid tank capacity | 100L |
capacity of the diagnostic fluid tank | 55L |
maximum temperature of the cleaning fluid | 50˚C |
type of connection of hydraulic hoses | 12x G1/2" |
mains water connection type | 1x G1/2″, 1x G3/4″ |
type of compressed air connection | EURO standard profile 26 series RQS |
control panel | 10.1" touch panel controller, |
weight of the device (without liquids) | 415kg |
maximum sound level | 83dB |
--installed power | 3 kW (1 heater) |
supply voltage | 400 VAC (three phases) |
power consumption | 13A |
CA-2
number of cleaning sections | 2 |
base medium | water |
Approved cleaning agent | depending on the type of sludge (DS1, DS2) |
diagnostic agent | Water + corrosion inhibitor (optional) |
type of diagnostic pump | rotor |
type of pump supplying the cleaning medium | Membrane (x2) |
type of pulsators | Membrane (x2) |
maximum capacity of the diagnostic pump | 73L/min |
Pump capacity per cleaning medium | 15L/min |
required air pressure | 8 Bar |
air consumption | 380L/min |
cleaning fluid tank capacity | 100L |
capacity of the diagnostic fluid tank | 55L |
maximum temperature of the cleaning fluid | 50˚C |
type of connection of hydraulic hoses | 4x G1/2" |
mains water connection type | 1x G1/2″, 1x G3/4″ |
type of compressed air connection | EURO standard profile 26 series RQS |
control panel | 10.1" touch panel controller, |
weight of the device (without liquids) | 275kg |
maximum sound level | 75dB |
--installed power | 3 kW (1 heater) |
supply voltage | 400 VAC (three phases) |
power consumption | 10A |
Dimensions of the device
CA-6
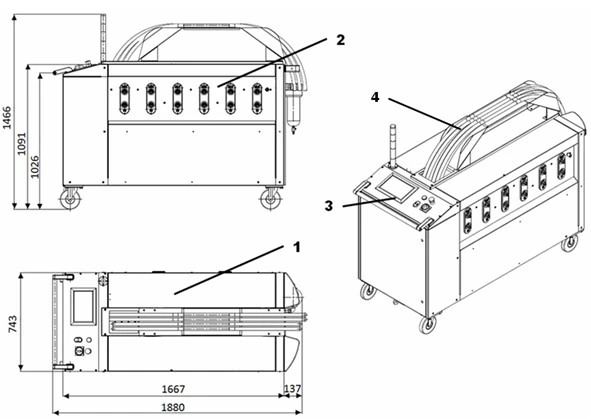
1 - tank section, 2 - mold connection section, 3 - control section, 4 - hydraulic hose tray
CA-2
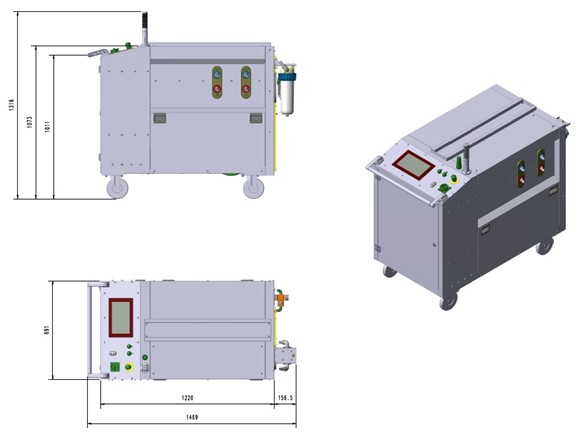
1 - tank section, 2 - mold connection section, 3 - control section

CM Series
The CM series of machines are versatile, customizable units that can be equipped with virtually all necessary functions according to the user's needs.
The proposed capacities of pumps and cavitation generators, allow you to choose the optimal device adapted to the size of the molds and the system of manifolds splicing the cooling channels. In addition, the chemistry tanks can be equipped with 6kW heaters, and cleaning is carried out bi-directionally, which significantly speeds up the process.
Highlights of the series:
Feature | Function | Benefit |
---|---|---|
Intuitive interface with built-in tutorials | The operator is informed step by step what sequence of operations he has to perform to run the given process | Machine easy to use, fast operator deployment time |
Automatic change of flow direction called from the desktop | Higher efficiency and uniformity of the cleaning process, no need to rewire hoses manually | Channels are clean on all sides, regardless of their length, less involvement on the part of the operator |
Diaphragm pump equipped with fiber optic sensors that measure the amount of diaphragm excursion over time | Real-time flow measurement function during cleaning | Shorter time of the whole operation, no risk of mixing liquids |
Optional section 7 with cavitation generator | Possibility to use the phenomenon of cavitation for cleaning heavily contaminated circuits | Higher dynamics and cleaning efficiency, shorter operation time |
6kW flow heating module | No heating elements in the tank, higher cleaning efficiency due to increased temperature | Easy access to the bottom of the tank, the operator is not in contact with the heating element, shorter cleaning time |
Feature
Intuitive interface with built-in tutorials
Automatic change of flow direction called from the desktop
Diaphragm pump equipped with fiber optic sensors that measure the amount of diaphragm excursion over time
Optional section 7 with cavitation generator
6kW flow heating module
Function
The operator is informed step by step what sequence of operations he has to perform to run the given process
Higher efficiency and uniformity of the cleaning process, no need to rewire hoses manually
Real-time flow measurement function during cleaning
Possibility to use the phenomenon of cavitation for cleaning heavily contaminated circuits
No heating elements in the tank, higher cleaning efficiency due to increased temperature
Benefit
Machine easy to use, fast operator deployment time
Channels are clean on all sides, regardless of their length, less involvement on the part of the operator
Shorter time of the whole operation, no risk of mixing liquids
Higher dynamics and cleaning efficiency, shorter operation time
Easy access to the bottom of the tank, the operator is not in contact with the heating element, shorter cleaning time
CME-7 / CME-5
Six-speed system (with optional seventh additional CAVI circuit)
CMS
Expansion module forCM series machines
CS series
The CM series of machines are versatile, customizable units that can be equipped with virtually all necessary functions according to the user's needs.
The proposed capacities of pumps and cavitation generators, allow you to choose the optimal device adapted to the size of the molds and the system of manifolds splicing the cooling channels. In addition, the chemistry tanks can be equipped with 6kW heaters, and cleaning is carried out bi-directionally, which significantly speeds up the process.
Highlights of the series:
Feature | Function | Benefit |
---|---|---|
Patented hydromechanical cleaning method using cavitation effect | Shorter cleaning time, cleaning agents used only to soften scale | Less risk of mold damage, more molds cleaned at the same time |
Two independent cleaning sections with dedicated feed pump and cavitation generator | Higher cleaning efficiency, more channels cleaned simultaneously, no bridging of channels required | More molds cleaned in the same time, higher cost/performance ratio |
Reversing the direction of flow of the cleaning medium | Equal cleaning dynamics on both sides of the channel | Greater cleaning efficiency when channels are connected in series |
Built-in tutorial mode, easy-to-use interface | Operators simply follow the directions displayed on the PLC screen | Fast learning curve for operators, low risk of error during machine setup |
Precise real-time liquid level monitoring with ultrasonic probe | Leakage / overflow protection with configurable alarm trigger values | Reduced risk of mold damage in case of sudden leakage |
Feature
Patented hydromechanical cleaning method using cavitation effect
Two independent cleaning sections with dedicated feed pump and cavitation generator
Reversing the direction of flow of the cleaning medium
Built-in tutorial mode, easy-to-use interface
Precise real-time liquid level monitoring with ultrasonic probe
Function
Shorter cleaning time, cleaning agents used only to soften scale
Higher cleaning efficiency, more channels cleaned simultaneously, no bridging of channels required
Equal cleaning dynamics on both sides of the channel
Operators simply follow the directions displayed on the PLC screen
Leakage / overflow protection with configurable alarm trigger values
Benefit
Less risk of mold damage, more molds cleaned at the same time
More molds cleaned in the same time, higher cost/performance ratio
Greater cleaning efficiency when channels are connected in series
Fast learning curve for operators, low risk of error during machine setup
Reduced risk of mold damage in case of sudden leakage
CS-2
Two-speed semi-automatic system
Detailed information
Functionality
Cleaning
Hydromechanical hybrid cleaning process based on the phenomenon of cavitation
A patented cleaning method that uses the phenomenon of cavitation to increase cleaning efficiency. The high dynamics of the cleaning process allows the mechanical removal of scale deposits, while the cleaning medium solution only aims to soften the contaminants adhering to the surface of the channel. Such a solution has many advantages. The channels are cleaned for a much shorter period of time, thus minimizing the contact time between the tool and the cleaning medium. In addition, we can use agents of lower concentration, which also minimizes the risk of damage to the mold in case of contact between the tool and the cleaning fluid.
Changing the direction of flow
Flow reversal can be useful if an operator decides to combine multiple channels and connect them to a single cleaning section. In this case, flow reversal can minimize the risk of an uneven cleaning process
Drying the channel after cleaning
The blowdown must be performed manually by the operator, who follows the sequence of steps given in the instructions or shown to him on the PLC screen
Possible export of mold cleaning results
CS devices keep records only of the most recent project, and the creation of the next one overwrites the previous one. However, it is possible to rip historical results for all projects to a mobilen device via hotspot.
Diagnostics
Leakage and patency test using compressed air
Flow reversal can be useful if an operator decides to combine multiple channels and connect them to a single cleaning section. In this case, flow reversal can minimize the risk of an uneven cleaning process
Drying the ducts with compressed air after the diagnostics are completed
The blowdown must be performed manually by the operator, who follows the sequence of steps given in the instructions or shown to him on the PLC screen
Maintenance
Flushing the sewers with mains water
A patented cleaning method that uses the phenomenon of cavitation to increase cleaning efficiency. The high dynamics of the cleaning process allows the mechanical removal of scale deposits, while the cleaning medium solution only aims to soften the contaminants adhering to the surface of the channel. Such a solution has many advantages. The channels are cleaned for a much shorter period of time, thus minimizing the contact time between the tool and the cleaning medium. In addition, we can use agents of lower concentration, which also minimizes the risk of damage to the mold in case of contact between the tool and the cleaning fluid.
Neutralization of cleaning agent residue in channels after cleaning
Flushing the ducts after the cleaning process is intended to flush out any residual cleaning agent from the ducts. This can be done either by an external water supply or by using a second tank with water mixed with corrosion inhibitors. If there is no external water supply, the operator must regularly change the water in the second tank, as its pH value will drop with each flushing. This will cause the water to be acidic and therefore unsuitable for neutralizing channels.
Possibility of additional protection of channels with corrosion inhibitor
Thanks to a unique design in which each section is equipped with a dedicated set of feeding pumps and cavitation generators, the machine can define an individual cleaning time for each channel based on historical flow expenses or stabilization of current expenses.
The machine, operating in automatic mode, itself compares the current results with the reference flow previously stored in the database. When the current measurement is a percentage close, the cleaning process for that section will end. Each channel can reach the desired flow at different times, so having separate pumps in each section is key to enabling this function. The set % to be achieved can be individually determined by the operator.
Additional features
Tank filling and emptying function
Thanks to the use of an ultrasonic probe in CA and CS machines, we have the possibility of precise, automatic filling of tanks. As a result, we have the same amount of liquid in the tank each time, which allows us to prepare the exact concentration of the cleaning solution. In the case of manual filling, the amount in the liquid in the tank may vary.
Suction filter clogging sensors
It allows real-time monitoring of how clogged the filters are. The machine itself informs the operator when they need to be cleaned, so the operator doesn't have to guess when it's time to do so.
Ability to modify parameters and algorithms of operation
The user can modify all the parameters of the device's operation, and can activate lud deactivate individual functions in automatic mode.
Choice of language version
Ability to switch between English, German, Spanish, French, Italian and Polish
Measurement of the pH and conductivity of the cleaning medium
Measuring tools dedicated to the machine make it possible to assess the level of overwork of the cleaning medium.
Security
System of sensors and algortms to ensure stable and safe operation
- Pre-blowdown algorithm (ramp) - protects the baffle from sudden pressure release, the pressure builds up gradually so that we minimize the risk of damage to the baffles and other components of the cooling system.
- Algorithm for verifying the correctness of readings from all pressure sensors - allows you to verify the presence of residual pressure in the system, which eliminates the possibility of backflow of liquid into the pneumatic system when changing the position of valves
- The machine informs the operator of the presence of residual pressure in the system, so he can drop it manually and safely unhook the hoses
- Each valve has a position control sensor - thanks to this feature, the operator has no possibility of starting the machine in the wrong configuration
- Algorithm for identifying the problem of obstruction of the circuit if the operator misses the patency test - in a situation where the flow rate is very low during the diagnostics, the machine will inform the operator of a potential obstruction and exclude the section in automatic operation mode. If there is a duct obstruction, it should be cleaned individually in manual mode.
Monitoring of cleaning fluid leakage during cleaning
An ultrasonic probe in the wash tank allows precise real-time measurement of the liquid level. The operator can define an acceptable volume drop that does not cause an alarm. It can be as low as 10 mm (equivalent to about 1 liter of liquid). If the liquid level in the tank drops by this value, the machine will automatically stop the process and send the operator an SMS message with information about a possible leak.
Controlling the level of solution in the tank
It can be a precision measurement (the ultrasonic probe measures the exact amount of liquid) or a float measurement, which gives a rough estimate.
Temperature control of the solution in the tank
Temperature sensors (one in the heater, the other on the filter housing).
Inspection of damage to heating elements
The machine has protection in the form of a thermostat located on the heating element, as well as software protection, which disconnects heating if the permissible temperature is exceeded.
Control of faulty phase connection
The machine detects the absence of any of the phases or the wrong order of their connection, this prevents damage to the impeller pump.
Control of the continuity of the medium flow through the heater system
The flow heating system is connected to a dedicated diaphragm pump that forces the fluid to circulate through the tank in which the heater is placed. An algorithm verifies that the heating element is fully immersed in the liquid and that the flow rate of that liquid is appropriate.
The machine, operating in automatic mode, itself compares the current results with the reference flow previously stored in the database. When the current measurement is a percentage close, the cleaning process for that section will end. Each channel can reach the desired flow at different times, so having separate pumps in each section is key to enabling this function. The set % to be achieved can be individually determined by the operator.
Air system moisture sensor
If the presence of water is detected in the compressed air, the machine will block the possibility of further operation. This is to protect the machine's pneumatic system, which is the most sensitive component of the entire design.
Service
- Modular design for easy component replacement
Technical data
Function | Value |
---|---|
Mode of operation | semi-automatic |
Power supply | 3x400V AC |
Controls/touchscreen | 7" |
number of circuits | 28 |
tank for cleaning medium | 0L |
tank for diagnostic medium | 25L |
Diaphragm pumps (L/min) | 252x25 |
Cavitation generator (L/min) | 6kW |
flow heater | yes |
filter on suction | yes |
filter on the return | yes |
CLEANING | |
Hydromechanical hybrid cleaning process based on the phenomenon of cavitation | yes |
cleaning process based on single-state pulsed feeding of cleaning liquid into the system | - |
diversion | yes |
Autonomous cleaning mode until stable reference expenditures are reached | - |
The cleaning time for each channel is defined independently. The process takes as long as necessary. | - |
Drying the canal after cleaning | manual |
DIAGNOSTICS | |
Possible export of mold cleaning results | yes |
Record of mold cleaning history in the machine database | - |
Modular design for easy component replacement | yes |
Leakage test using compressed air | yes |
Compressed air patency test | - |
Automatic diagnostics with maintenance-free transition to cleaning mode | - |
Measurement of flow expenditure with the possibility of reference to reference expenditures stored in the database | - |
Real-time flow rate measurement | yes |
CONSERVATION | |
Drying the ducts with compressed air after the diagnostics are completed | yes |
Flushing the sewers with mains water | yes |
Neutralization of cleaning agent residue in channels after cleaning | yes |
ADDITIONAL FUNCTIONS | |
Possibility of additional protection of channels with corrosion inhibitor | yes |
Tank filling and emptying function | yes |
Modular design for easy component replacement | - |
suction filter clogging sensors | yes |
ability to calibrate parameters and work algorithms | yes |
Record of the number of operating hours for individual pumps and pulsators | - |
Monitoring the number of operating hours for the cleaning medium | - |
Remote software update | yes |
Ability to create user accounts with different levels of access to machine functions | yes |
Choice of language version | yes |
SECURITY | |
Built-in sink drain for emergency emptying of tanks | manual |
control of the efficiency of the compressed air source | not |
forgetting the pH and conductivity of the cleaning medium | yes |
OPC UA module | yes |
a system of sensors and algorithms to ensure stable and safe operation | yes |
Monitoring of cleaning fluid leakage during cleaning | yes |
Controlling the level of solution in the tank | yes |
Temperature control of the solution in the tank | yes |
Inspection of damage to heating elements | - |
SERVICE | |
Control of faulty phase connection | yes |
Control of the continuity of the medium flow through the heater system | yes |
additional protection against tank damage and leakage | - |
air system moisture sensor | yes |
Modular design for easy component replacement | yes |
Ability to remotely assess the cause of equipment failure at the customer's site | - |
Evaluation of the correct operation of the filter clogging sensors | yes |
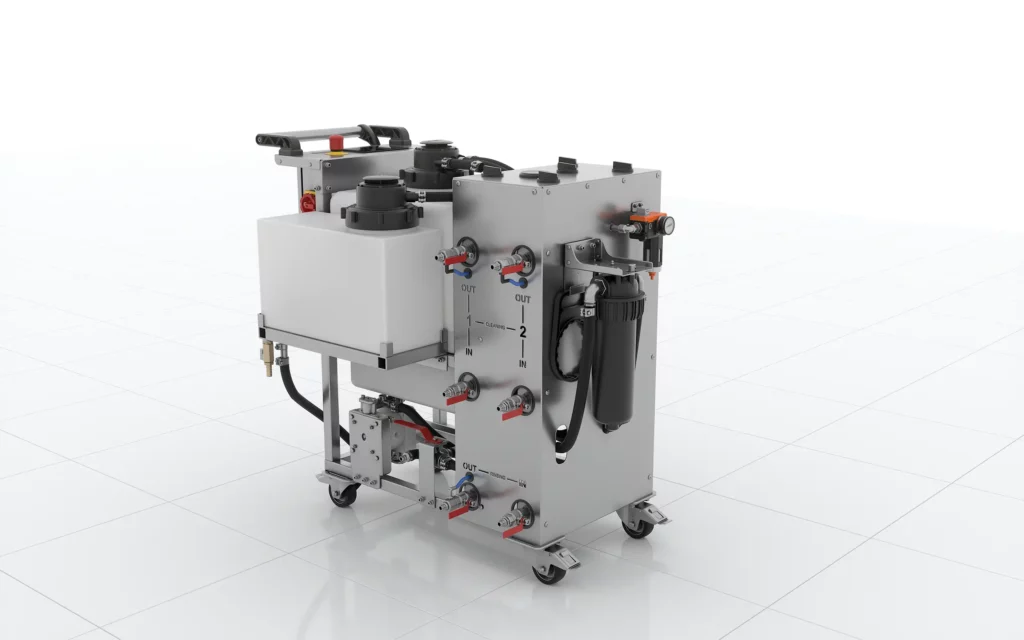
CP series
CP series - compact, affordable units. Ideal for production facilities with a small number of molds. CP units are based on the same cleaning technology as the higher-end CoolingCare models.
CP-2 DUO
Two-circuit system with additional tank for flushing channels after cleaning
CP-1
Single-circuit system equipped with tank and compact cleaning module
CP CASE
Single-circuit, compact cleaning module without collector