Machines for diagnostics, maintenance and cleaning of water circuits
Injection molding
Die casting
Other heat exchangers
Application of CoolingCare technology
Injection molding
Die casting
Other heat exchangers
From basic constructions to sophisticated units
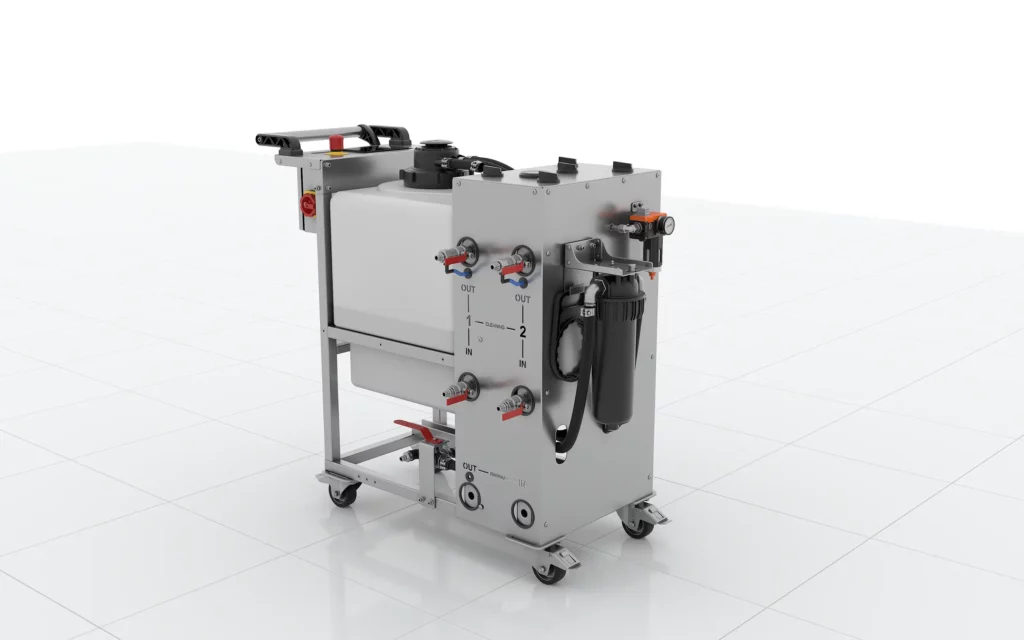
CP series
CP series - compact, affordable devices. Perfect for production plants with few molds. CP devices are based on the same cleaning technology as the higher-end CoolingCare models.

CM series
The CM series of machines are universal, configurable units that can be equipped with virtually all necessary functions according to the user's needs.
The proposed capacities of pumps and cavitation generators allow you to choose the optimal device adapted to the size of the molds and the system of collectors connecting the cooling channels. Additionally, chemical tanks can be equipped with 6kW heaters, and cleaning takes place in two directions, which significantly speeds up the process.
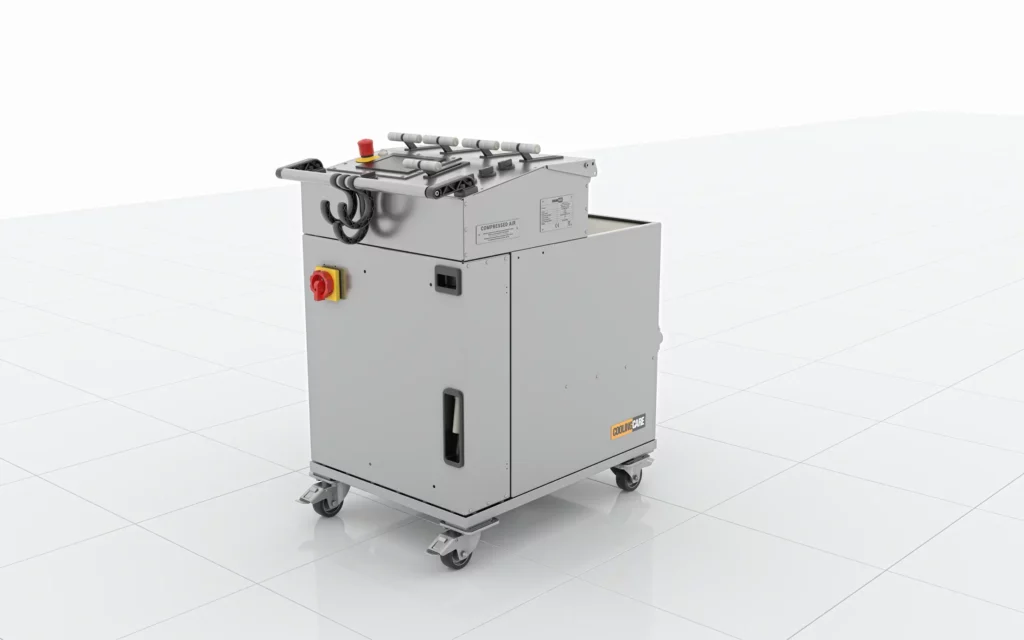
CS series
The CS2 machine is the smallest in the series intended for users with the highest demands. It is equipped with all the necessary functions known from flagship CA machines, apart from the mold database and the ability to communicate via OPC UA.
CS2 is produced only in a two-circuit version with a semi-automatic operating mode. Intuitive and user-friendly software allows for very quick implementation of staff and starting work without preliminary training.
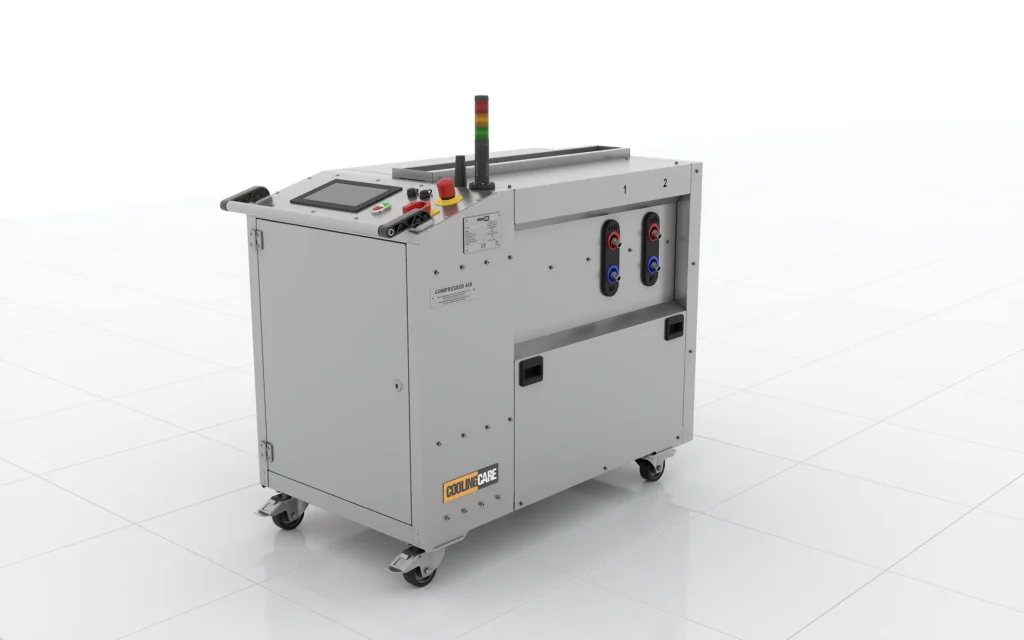
CA series
CA series devices are the most advanced systems in the CoolingCare family. These fully automated machines have been designed to meet the highest demands in the modern plastics production environment.
They are packed with features that allow users to monitor and maintain full control of the cooling performance of their molds.
From basic constructions to sophisticated units
Budget
CP series
CP series - compact, affordable devices. Perfect for production plants with few molds. CP devices are based on the same cleaning technology as the higher-end CoolingCare models.
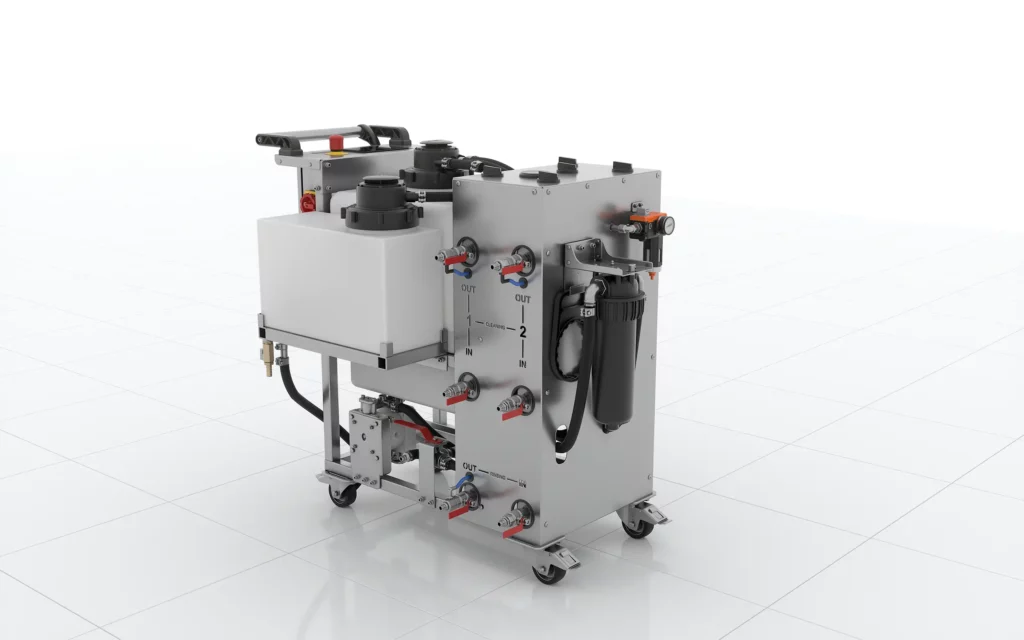
Classic
CM series
The CM series of machines are universal, configurable units that can be equipped with virtually all necessary functions according to the user's needs. The proposed capacities of pumps and cavitation generators allow you to choose the optimal device adapted to the size of the molds and the system of collectors connecting the cooling channels. Additionally, chemical tanks can be equipped with 6kW heaters, and cleaning takes place in two directions, which significantly speeds up the process.

Premium
CA series
CA series devices are the most advanced systems in the CoolingCare family. These fully automated machines have been designed to meet the highest demands in the modern plastics production environment. They are packed with features that allow users to monitor and maintain full control of the cooling performance of their molds.
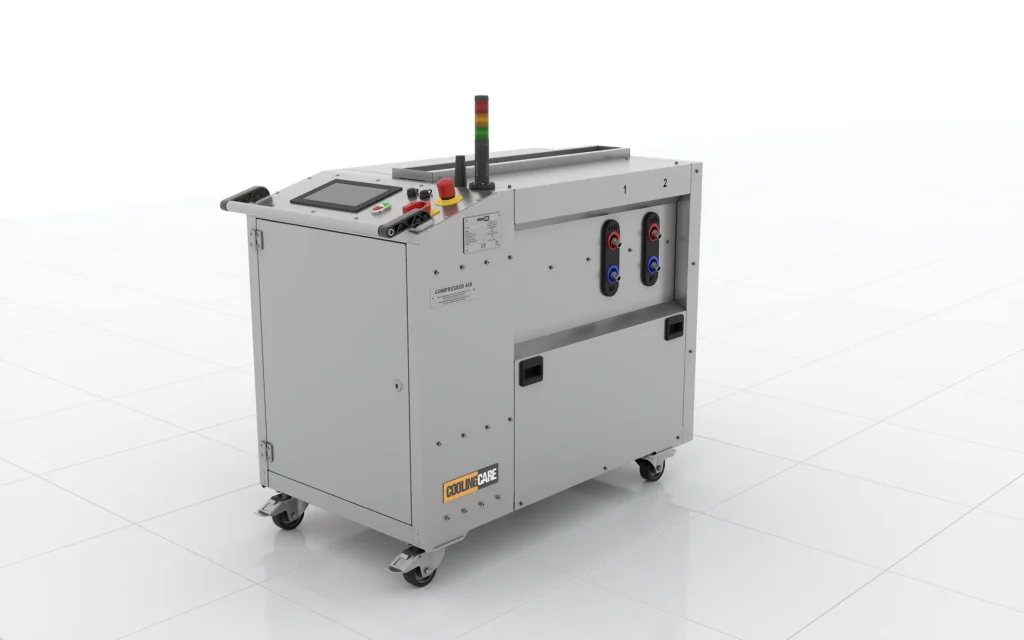
Premium
CS series
The CS2 machine is the smallest in the series intended for users with the highest demands. It is equipped with all the necessary functions known from flagship CA machines, apart from the mold database and the ability to communicate via OPC UA. CS2 is produced only in a two-circuit version with a semi-automatic operating mode. Intuitive and user-friendly software allows for very quick implementation of staff and starting work without preliminary training.
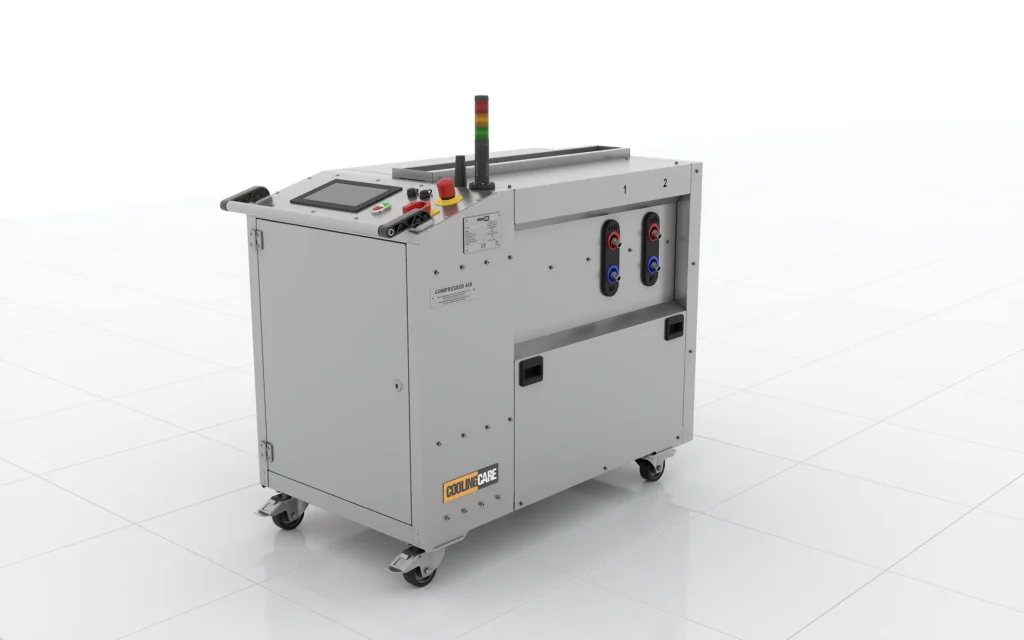
Why choose CoolingCare?
Cleaning time
is up to several times shorter than conventional methods.
Less aggressive cleaning agents
and shorter time of mold exposure to chemicals - lower risk of tool damage.
Thanks to advanced automation
and work algorithms, operator interaction is limited to a minimum.
The device itself performs
a sequence of operations in accordance with the selected work algorithm, and then generates a report that is saved in the device database.
At the same time, sensors and safety algorithms ensure
the correct operation of the device; if any anomaly occurs, the process is put on hold and the operator is informed of the event via text message.
Top quality materials
Each element of our machines has been carefully selected to meet the challenges of working with aggressive media. Before being approved, each element of the structure is subjected to rigorous fatigue and chemical tests.
Components from the best manufacturers
We use parts of our production in combination with components from recognized world leaders such as Keyence, SICK, WAGO, MetalWork, FESTO or R&R.
Advanced self-diagnostics systems
that inform the operator about potential irregularities or the need for inspection - minimizing the risk of unplanned downtime.
Rigid quality control
Each machine undergoes a series of strict approval procedures before being shipped to the customer. Such rigorous conditions provide peace of mind for us and our customers.
* - warranty extension available as a paid option
The machine itself identifies
the optimal flor rate for a given cycle or cleans until the reference flow saved in the database is reached.
The machine algorithm monitors
the cleaning process in real time and adapts the process parameters to the conditions in the channel.
Less risk of damaging the tool
the channel is in contact with the cleaning medium only until the contamination is removed.
Cleaning time only lasts
as long as necessary.
Dozens of sensors and algorithms
That control the correct and safe operation of the device for the injection mold.
If any irregularities occur
the computer stops the cleaning process and notifies the operator.
Why choose CoolingCare?
Cleaning time is up to several times shorter than conventional methods
Less aggressive cleaning agents and shorter time of mold exposure to chemicals - lower risk of tool damage
Thanks to advanced automation and work algorithms, operator interaction is limited to a minimum.
The device itself performs a sequence of operations in accordance with the selected work algorithm, and then generates a report that is saved in the device database.
At the same time, sensors and safety algorithms ensure the correct operation of the device; if any anomaly occurs, the process is put on hold and the operator is informed of the event via text message.
Top quality materials: Each element of our machines has been carefully selected to meet the challenges of working with aggressive media. Before being approved, each element of the structure is subjected to rigorous fatigue and chemical tests
Components from the best manufacturers: We use parts of our production in combination with components from recognized world leaders such as Keyence, SICK, WAGO, MetalWork, FESTO or B&R
Advanced self-diagnostics systems that inform the operator about potential irregularities or the need for inspection - minimizing the risk of unplanned downtime
Rigid quality control: Each machine undergoes a series of strict approval procedures before being shipped to the customer. Such rigorous conditions provide peace of mind for us and our customers
* - warranty extension available as a paid option
The machine itself identifies the optimal flor rate for a given cycle or cleans until the reference flow saved in the database is reached
The machine algorithm monitors the cleaning process in real time and adapts the process parameters to the conditions in the channel.
Less risk of damaging the tool, the channel is in contact with the cleaning medium only until the contamination is removed
Cleaning time only lasts as long as necessary
Dozens of sensors and algorithms that control the correct and safe operation of the device for the injection mold
If any irregularities occur, the computer stops the cleaning process and notifies the operator.
News and updates
FAKUMA 2024
COOLINGCARE at FAKUMA 2024 We are excited to announce that we will be exhibiting at the upcoming edition of FAKUMA 2024, one of the most important plastics events this year!
NPE 2024
Thank you to everyone who visited our booth at #NPE2024 in the United States! We were thrilled to showcase our innovative machines for cleaning cooling channels in injection molds. Special
PLASTPOL 2024
We invite you to visit our booth at the XXVIII International Fair of Plastics and Rubber Processing PLASTPOL 2024, which will be held on May 21-24, 2024 in Kielce. In
Coolingcare in numbers
Check the markets where we cooperate with local distributors