About us
Innovation born from necessity
CoolingCare machines were created in response to the challenges faced by modern injection molding plants, particularly in cleaning and diagnosing cooling channels in injection molds. This project was the result of more than six years of research conducted by FADO, a company with over 35 years of experience in mold manufacturing and the design of mold inserts with conformal cooling systems.
Conformal cooling, due to its complex geometry and small channel diameters, requires innovative approaches in both operation and maintenance. Despite its numerous advantages, these systems carry risks that deter many companies from investing in their development. The main concerns are the gradual decline in heat dissipation efficiency and the high susceptibility to clogging. In the event of a complete blockage, it is often impossible to mechanically clear the channel without disassembling the mold. This is why monitoring the condition of the cooling channels and applying appropriate preventive measures is crucial to maintaining their long-term efficiency.
Our tests have shown that conventional market devices, which rely on laminar flow cleaning methods, are ineffective in dealing with completely clogged channels. This is precisely why our R&D department developed cavitation cleaning technology, which proved to be so effective that we decided to commercialize it. Our goal was to create a device that not only cleans but also diagnoses and maintains cooling channels – fully addressing the needs of modern injection molding plants.
This is how the CA6 model was born, our flagship product, which quickly became a benchmark in the market. Over time, our product range expanded with additional models to meet the diverse needs of our customers. Today, our product line includes several devices, offering a full spectrum of solutions – from budget-friendly models to fully automated units
Toolroom
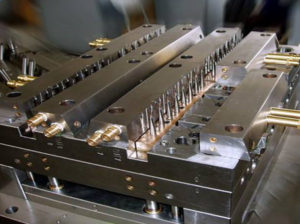
- Injection mold design and manufacturing
- Maximum mold dimensions: 500x500mm
- Machine park based on MAKINO machine tools
Injection molding
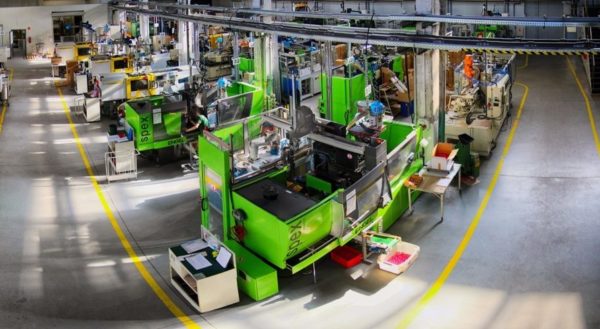
Injection molding machines with horizontal and vertical clamping forces ranging from 10 to 800 tons. The machines are fully adapted for automatic operation.
3D print
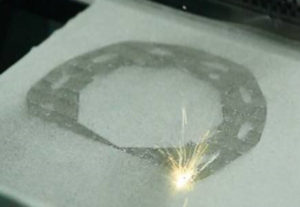
Laser powder bed fusion technology for manufacturing inserts with conformal cooling. Available materials: tool steel 1.2709, stainless steel 316L, AlSi10Mg, Ti64.
Toolroom
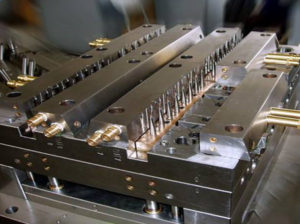
- Injection mold design and manufacturing
- Maximum mold dimensions: 500x500mm
- Machine park based on MAKINO machine tools
Injection molding
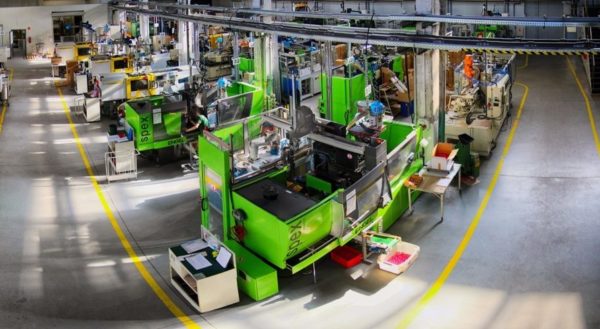
Injection molding machines with horizontal and vertical clamping forces ranging from 10 to 800 tons. The machines are fully adapted for automatic operation
3D print
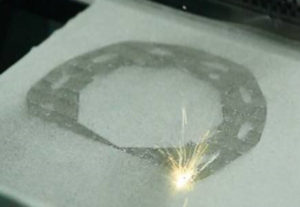
Laser powder bed fusion technology for manufacturing inserts with conformal cooling. Available materials: tool steel 1.2709, stainless steel 316L, AlSi10Mg, Ti64.
About company
FADO’s beginnings date back to 1984, when Jerzy Domeracki, continuing the family tradition in the tool industry, decided to start producing injection molds. In a short time, thanks to determination, passion and hard work, the plant began to achieve its first successes.
A breakthrough moment in the company’s history was 1991, and with it the decision to create a plastics processing department, thanks to which FADO’s business model underwent a dramatic change – the company was no longer just a tool manufacturer, it expanded its offer to include the production of plastic parts.
It turned out that the experience gained in mold design proved to be excellent in processing. In turn, the experience with plastic injection allowed for even better analysis of problems, and thus better design of the molds themselves.
Thanks to this experience, FADO has developed many original, innovative solutions that have allowed the company to build its position in the market. Commitment, continuous development and investment in new technologies have meant that over the years the company has been honored with many prestigious awards and titles, such as Forbes Diamonds, Innovation Leader or Business Gazelles. Today, details produced at FADO can be found on most continents around the world.