Porównywarka
CoolingCare CP
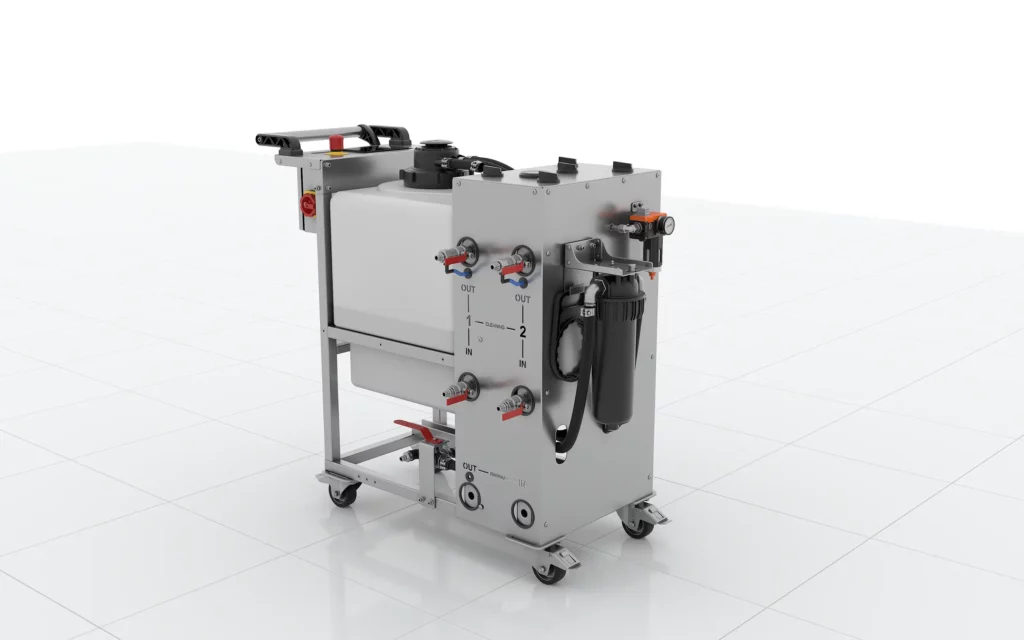
CP CASE | CP1 | CP2 | |
Mode of operation | ręczny | ||
Power supply | sprężone powietrze | 230 V AC | |
Controls/touchscreen | pneumatyczne | 3,5″ | |
number of circuits | 1 | 2 | |
tank for cleaning medium | – | 80L | 80L |
tank for diagnostic medium | – | ||
Diaphragm pumps (L/min) | 25 | ||
Cavitation generator (L/min) | 25 | 2×25 | |
flow heater | – | ||
filter on suction | – | yes | |
filter on the return | – | yes | |
CLEANING | |||
Hydromechanical hybrid cleaning process based on the phenomenon of cavitation | yes | ||
cleaning process based on single-state pulsed feeding of cleaning liquid into the system | – | ||
diversion | – | ||
Autonomous cleaning mode until stable reference expenditures are reached | – | ||
The cleaning time for each channel is defined independently. The process takes as long as necessary. | – | ||
osuszanie kanału po czyszczeniu, | manual | ||
Possible export of mold cleaning results | – | ||
Record of mold cleaning history in the machine database | – | ||
Modular design for easy component replacement | |||
DIAGNOSTICS | |||
Leakage test using compressed air | yes | ||
Compressed air patency test | yes | ||
Automatic diagnostics with maintenance-free transition to cleaning mode | – | ||
Measurement of flow expenditure with the possibility of reference to reference expenditures stored in the database | – | ||
Real-time flow rate measurement | – | ||
Drying the ducts with compressed air after the diagnostics are completed | – | ||
CONSERVATION | |||
Flushing the sewers with mains water | – | yes | |
Neutralization of cleaning agent residue in channels after cleaning | opcja (moduł CMS) | ||
Possibility of additional protection of channels with corrosion inhibitor | opcja (moduł CMS) | ||
ADDITIONAL FUNCTIONS | |||
Tank filling and emptying function | – | ||
Modular design for easy component replacement | yes | ||
suction filter clogging sensors | – | ||
ability to calibrate parameters and work algorithms | – | ||
Record of the number of operating hours for individual pumps and pulsators | – | ||
Monitoring the number of operating hours for the cleaning medium | – | ||
Remote software update | – | ||
Ability to create user accounts with different levels of access to machine functions | – | ||
Choice of language version | – | ||
Built-in sink drain for emergency emptying of tanks | – | yes | |
control of the efficiency of the compressed air source | – | ||
pomiar pH i konduktywności medium czyszczącego | manual | ||
OPC UA module | not | ||
SECURITY | |||
a system of sensors and algorithms to ensure stable and safe operation | – | ||
Monitoring of cleaning fluid leakage during cleaning | – | ||
Controlling the level of solution in the tank | – | ||
Temperature control of the solution in the tank | – | ||
Inspection of damage to heating elements | – | ||
Control of faulty phase connection | – | ||
Control of the continuity of the medium flow through the heater system | – | ||
additional protection against tank damage and leakage | – | ||
air system moisture sensor | – | ||
SERVICE | |||
Modular design for easy component replacement | yes | ||
Ability to remotely assess the cause of equipment failure at the customer's site | – | ||
Evaluation of the correct operation of the filter clogging sensors | – |
CoolingCare CS
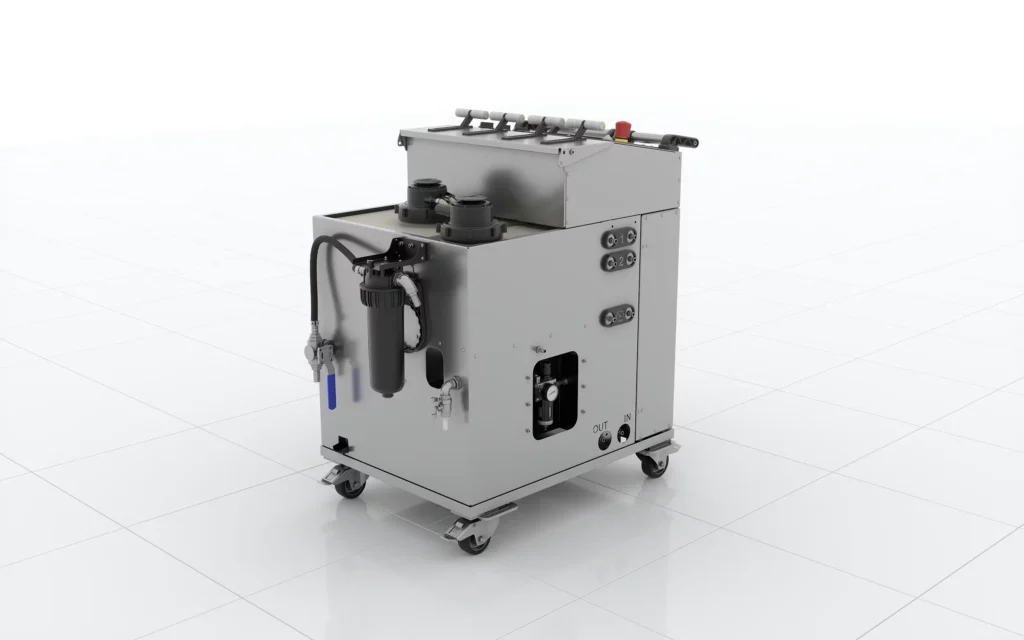
CS2 | |
Mode of operation | semi-automatic |
Power supply | 3x400V AC |
Controls/touchscreen | 7″ |
number of circuits | 2 |
tank for cleaning medium | 80L |
tank for diagnostic medium | 25L |
Diaphragm pumps (L/min) | 25 |
Cavitation generator (L/min) | 2×25 |
flow heater | 6kW |
filter on suction | yes |
filter on the return | yes |
CLEANING | |
Hydromechanical hybrid cleaning process based on the phenomenon of cavitation | yes |
cleaning process based on single-state pulsed feeding of cleaning liquid into the system | – |
diversion | yes |
Autonomous cleaning mode until stable reference expenditures are reached | – |
The cleaning time for each channel is defined independently. The process takes as long as necessary. | – |
osuszanie kanału po czyszczeniu, | manual |
Possible export of mold cleaning results | yes |
Record of mold cleaning history in the machine database | – |
Modular design for easy component replacement | |
DIAGNOSTICS | |
Leakage test using compressed air | yes |
Compressed air patency test | yes |
Automatic diagnostics with maintenance-free transition to cleaning mode | – |
Measurement of flow expenditure with the possibility of reference to reference expenditures stored in the database | – |
Real-time flow rate measurement | – |
Drying the ducts with compressed air after the diagnostics are completed | yes |
CONSERVATION | |
Flushing the sewers with mains water | yes |
Neutralization of cleaning agent residue in channels after cleaning | yes |
Possibility of additional protection of channels with corrosion inhibitor | yes |
ADDITIONAL FUNCTIONS | |
Tank filling and emptying function | yes |
Modular design for easy component replacement | yes |
suction filter clogging sensors | yes |
ability to calibrate parameters and work algorithms | – |
Record of the number of operating hours for individual pumps and pulsators | yes |
Monitoring the number of operating hours for the cleaning medium | yes |
Remote software update | – |
Ability to create user accounts with different levels of access to machine functions | – |
Choice of language version | yes |
Built-in sink drain for emergency emptying of tanks | yes |
control of the efficiency of the compressed air source | yes |
pomiar pH i konduktywności medium czyszczącego | manual |
OPC UA module | not |
SECURITY | |
a system of sensors and algorithms to ensure stable and safe operation | |
Monitoring of cleaning fluid leakage during cleaning | yes |
Controlling the level of solution in the tank | yes |
Temperature control of the solution in the tank | yes |
Inspection of damage to heating elements | yes |
Control of faulty phase connection | yes |
Control of the continuity of the medium flow through the heater system | yes |
additional protection against tank damage and leakage | – |
air system moisture sensor | yes |
SERVICE | |
Modular design for easy component replacement | yes |
Ability to remotely assess the cause of equipment failure at the customer's site | – |
Evaluation of the correct operation of the filter clogging sensors | yes |
CoolingCare CM
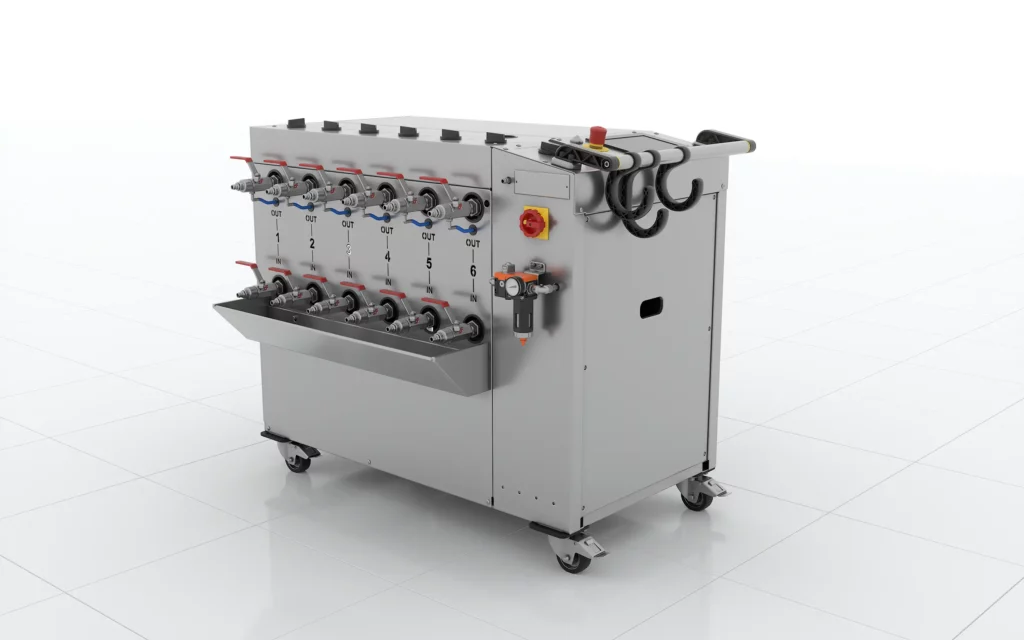
CM4 | CM6 | |
Mode of operation | ręczny | |
Power supply | 230 V AC | |
Controls/touchscreen | 7″ | |
number of circuits | 4 | 6 |
tank for cleaning medium | 80L | |
tank for diagnostic medium | opcja (moduł CMS) | |
Diaphragm pumps (L/min) | 70 | 70 (opcja 125) |
Cavitation generator (L/min) | ocjonalna, 5 lub7 sekcja z generatortem kawitacji | |
flow heater | 6kW (opcja) | |
filter on suction | yes | |
filter on the return | yes | |
CLEANING | ||
Hydromechanical hybrid cleaning process based on the phenomenon of cavitation | – | |
cleaning process based on single-state pulsed feeding of cleaning liquid into the system | yes | |
diversion | yes | |
Autonomous cleaning mode until stable reference expenditures are reached | – | |
The cleaning time for each channel is defined independently. The process takes as long as necessary. | – | |
osuszanie kanału po czyszczeniu, | manual | |
Possible export of mold cleaning results | yes | |
Record of mold cleaning history in the machine database | – | |
Modular design for easy component replacement | ||
DIAGNOSTICS | ||
Leakage test using compressed air | yes | |
Compressed air patency test | yes | |
Automatic diagnostics with maintenance-free transition to cleaning mode | – | |
Measurement of flow expenditure with the possibility of reference to reference expenditures stored in the database | – | |
Real-time flow rate measurement | yes | |
Drying the ducts with compressed air after the diagnostics are completed | yes | |
CONSERVATION | ||
Flushing the sewers with mains water | yes | |
Neutralization of cleaning agent residue in channels after cleaning | opcja (moduł CMS) | |
Possibility of additional protection of channels with corrosion inhibitor | opcja (moduł CMS) | |
ADDITIONAL FUNCTIONS | ||
Tank filling and emptying function | yes | |
Modular design for easy component replacement | yes | |
suction filter clogging sensors | – | |
ability to calibrate parameters and work algorithms | – | |
Record of the number of operating hours for individual pumps and pulsators | – | |
Monitoring the number of operating hours for the cleaning medium | – | |
Remote software update | – | |
Ability to create user accounts with different levels of access to machine functions | – | |
Choice of language version | yes | |
Built-in sink drain for emergency emptying of tanks | yes | |
control of the efficiency of the compressed air source | – | |
pomiar pH i konduktywności medium czyszczącego | manual | |
OPC UA module | not | |
SECURITY | ||
a system of sensors and algorithms to ensure stable and safe operation | – | |
Monitoring of cleaning fluid leakage during cleaning | – | |
Controlling the level of solution in the tank | – | |
Temperature control of the solution in the tank | – | |
Inspection of damage to heating elements | – | |
Control of faulty phase connection | – | |
Control of the continuity of the medium flow through the heater system | – | |
additional protection against tank damage and leakage | – | |
air system moisture sensor | – | |
SERVICE | ||
Modular design for easy component replacement | ||
Ability to remotely assess the cause of equipment failure at the customer's site | ||
Evaluation of the correct operation of the filter clogging sensors |
CoolingCare CA
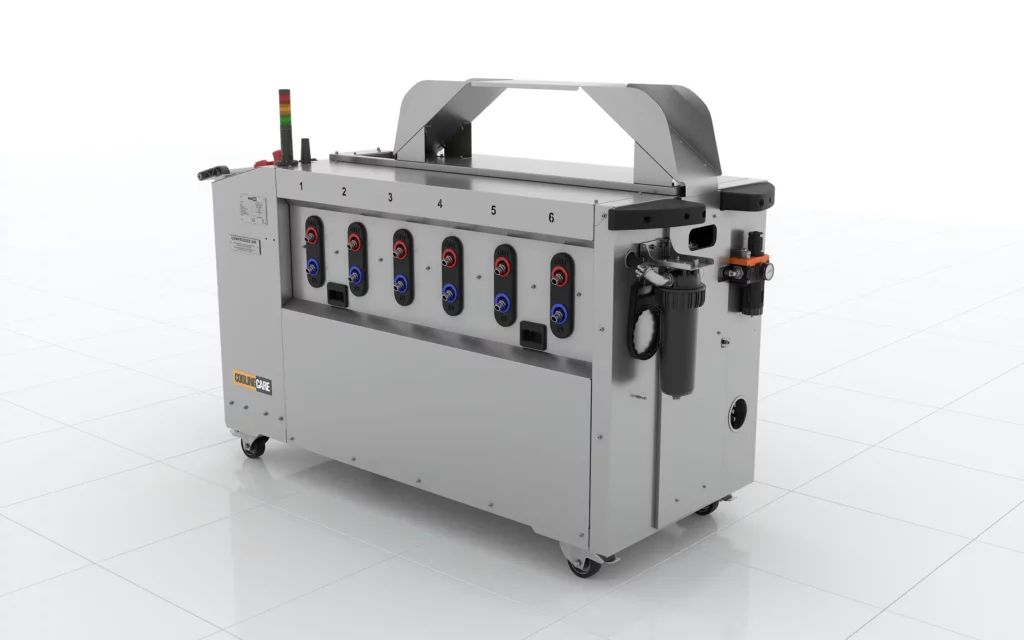
CA2 | CA6 | |
Mode of operation | automat | |
Power supply | 3x400V AC | |
Controls/touchscreen | 10″ | |
number of circuits | 2 | 6 |
tank for cleaning medium | 100L | |
tank for diagnostic medium | 55L | |
Diaphragm pumps (L/min) | 2×25 | 4×25 |
Cavitation generator (L/min) | 2×25 | 6×25 |
flow heater | 6kW | |
filter on suction | yes | |
filter on the return | yes | |
CLEANING | ||
Hydromechanical hybrid cleaning process based on the phenomenon of cavitation | yes | |
cleaning process based on single-state pulsed feeding of cleaning liquid into the system | – | |
diversion | – | |
Autonomous cleaning mode until stable reference expenditures are reached | yes | |
The cleaning time for each channel is defined independently. The process takes as long as necessary. | yes | |
osuszanie kanału po czyszczeniu, | automatyczne | |
Possible export of mold cleaning results | yes | |
Record of mold cleaning history in the machine database | yes | |
Modular design for easy component replacement | ||
DIAGNOSTICS | ||
Leakage test using compressed air | yes | |
Compressed air patency test | yes | |
Automatic diagnostics with maintenance-free transition to cleaning mode | yes | |
Measurement of flow expenditure with the possibility of reference to reference expenditures stored in the database | yes | |
Real-time flow rate measurement | – | |
Drying the ducts with compressed air after the diagnostics are completed | yes | |
CONSERVATION | ||
Flushing the sewers with mains water | yes | |
Neutralization of cleaning agent residue in channels after cleaning | yes | |
Possibility of additional protection of channels with corrosion inhibitor | yes | |
ADDITIONAL FUNCTIONS | ||
Tank filling and emptying function | yes | |
Modular design for easy component replacement | yes | |
suction filter clogging sensors | yes | |
ability to calibrate parameters and work algorithms | yes | |
Record of the number of operating hours for individual pumps and pulsators | yes | |
Monitoring the number of operating hours for the cleaning medium | yes | |
Remote software update | yes | |
Ability to create user accounts with different levels of access to machine functions | yes | |
Choice of language version | yes | |
Built-in sink drain for emergency emptying of tanks | yes | |
control of the efficiency of the compressed air source | yes | |
pomiar pH i konduktywności medium czyszczącego | manual | |
OPC UA module | yes | |
SECURITY | ||
a system of sensors and algorithms to ensure stable and safe operation | yes | |
Monitoring of cleaning fluid leakage during cleaning | yes | |
Controlling the level of solution in the tank | yes | |
Temperature control of the solution in the tank | yes | |
Inspection of damage to heating elements | yes | |
Control of faulty phase connection | yes | |
Control of the continuity of the medium flow through the heater system | yes | |
additional protection against tank damage and leakage | yes | |
air system moisture sensor | yes | |
SERVICE | ||
Modular design for easy component replacement | yes | |
Ability to remotely assess the cause of equipment failure at the customer's site | yes | |
Evaluation of the correct operation of the filter clogging sensors | yes |